Semi centrifugal casting is a specialized metal casting process that combines gravity pouring with centrifugal force to produce high-quality castings.
It is one of the types of centrifugal castings. The semi centrifugal casting process is used to produce complex-shaped parts with internal features.
Let’s learn more about it.
This article will help you get more information about,
- What is Semi Centrifugal Casting ?
- Semi Centrifugal Casting Process:
- Advantages and Disadvantages of Semi Centrifugal Casting:
- Advantages of Semi Centrifugal Casting:
- Disadvantages of Semi Centrifugal Casting:
- Applications of Semi Centrifugal Castings:
- How TOPGRID can help you ?
What is Semi Centrifugal Casting ?
Semi centrifugal casting is a metal casting process. Through a central sprue, the molten metal is partially filled into a rotating mold. The rotating mold creates centrifugal force which distributes the metal throughout the mold cavity. This creates a dense and defect-free casting.
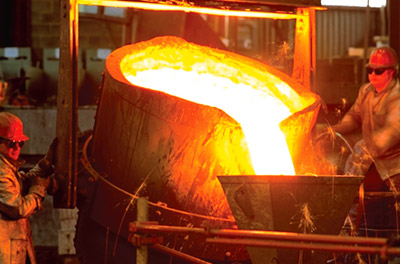
If you’re intending to choose this method of casting process, you must know about the process yourself. This concise guide will give you an overview of the step-by-step process of semi centrifugal casting.
Semi Centrifugal Casting Process:
The step-by-step process of semi centrifugal casting process,
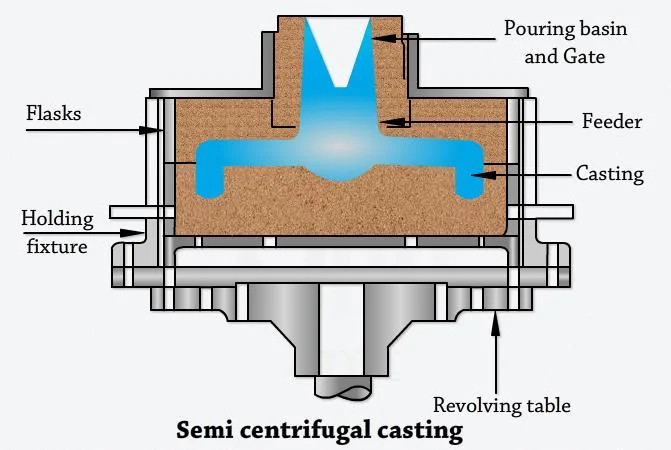
Step:1
Mold Preparation:
The process starts with the mold preparation. A cope and drag mold is prepared using sand or metal. A central sprue is placed at the top of the mold for pouring molten metal. If the casting requires a central bore, a dry sand core is inserted.
Then, the mold is mounted securely on a rotating table.
Step:2
Melting the Metal:
The metal alloy (generally, iron, aluminum, or copper alloys) is heated to its molten state in a separate furnace. The metal is maintained at the appropriate temperature for casting.
Step: 3
Metal Pouring:
The mold is preheated to an appropriate temperature. The table starts rotating at a predetermined speed. Then the molten metal is poured into the central sprue.
Step:4
Centrifugal filling:
The rotation of the mold generates centrifugal force. Centrifugal force pushes the molten metal outward. This coats the inner surface of the mold.
Step:5
Solidification:
The rotation speed is maintained until the molten metal solidifies completely. The rotation is stopped once the solidification is completed.
Step:6
Cooling and Removing:
The casting is allowed to cool gradually inside the mold. Once cooled, the casting is removed from the mold. And, if present, the sand core broke away.
Finishing operations, such as cleaning, grinding, or machining are performed if necessary.
Hence these are the steps involved in the semi centrifugal casting process.
And, learning about more such casting processes, like Gravity die casting, High-pressure die casting, and Low-pressure die casting will help you gain vast knowledge about overall casting processes.
This helps you in better decision-making while choosing the right one for your project. Now let’s look into the advantages and disadvantages of semi centrifugal casting.
Advantages and Disadvantages of Semi Centrifugal Casting:
When choosing a casting process you need to consider both the advantages and disadvantages of it. That helps you in minimizing costs and ensuring the quality of your products.
Here are a few advantages and disadvantages of the semi centrifugal casting process.
Advantages of Semi Centrifugal Casting:
A few advantages of semi centrifugal casting are,
- Centrifugal force ensures complete filling of the mold, even for intricate shapes and thin sections. This reduces the risk of shrinkage, porosity, and incomplete castings.
- The centrifugal force promotes the separation of impurities and gasses. This results in denser and stronger castings with improved mechanical properties.
- The semi centrifugal casting process produces casting with a smoother surface finish. Therefore requires less machining and polishing.
- Semi centrifugal casting is compatible with a wide variety of ferrous and non-ferrous metals and alloys.
- The process is faster than traditional gravity casting methods. This leads to higher production rates.
- Compared to true centrifugal casting, the semi centrifugal casting process requires lower rotation speeds. This results in less equipment wear and tear. This may also results in lower energy consumption.
Disadvantages of Semi Centrifugal Casting:
Here are a few semi centrifugal casting disadvantages,
- It is best suited for axially symmetrical shapes. Hence can be challenging for complex geometries with intricate internal features.
- This process can lead to some porosity and inclusion, particularly near the central axis of the casting (less compared to gravity casting).
- The machinery required for this casting method can be more expensive than for simpler casting methods.
- While the outer surface of the casting is highly accurate, the inner diameter may require additional machining to achieve accurate dimensions.
- Working with molten metal and rotating equipment in this casting process requires strict safety protocols and trained personnel.
Applications of Semi Centrifugal Castings:
Semi centrifugal casting is a versatile process used to manufacture various parts in different industries.
Here are some of its applications:
Automotive:
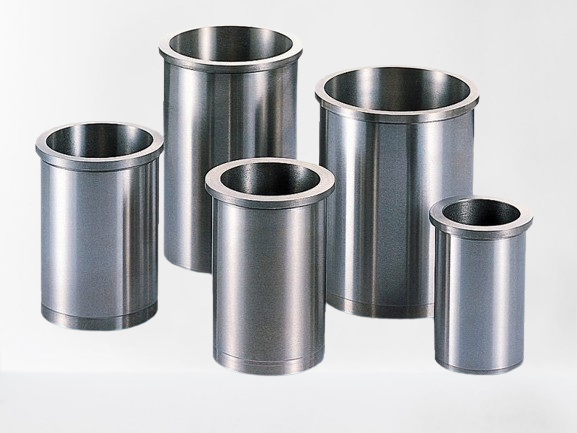
- Rims
- Hubs
- Pistons
- Brake drums
- Cylinder liners
- Connecting rods
Aerospace:
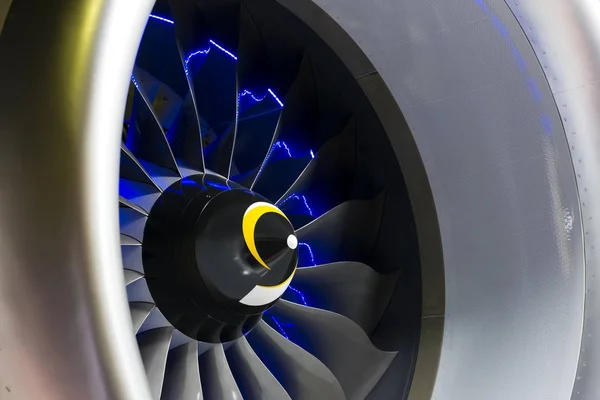
- Turbine blades
- Landing gear struts
Oil and Gas:

- Pipes
- Valves
- Impellers
- Pump housings
General Engineering
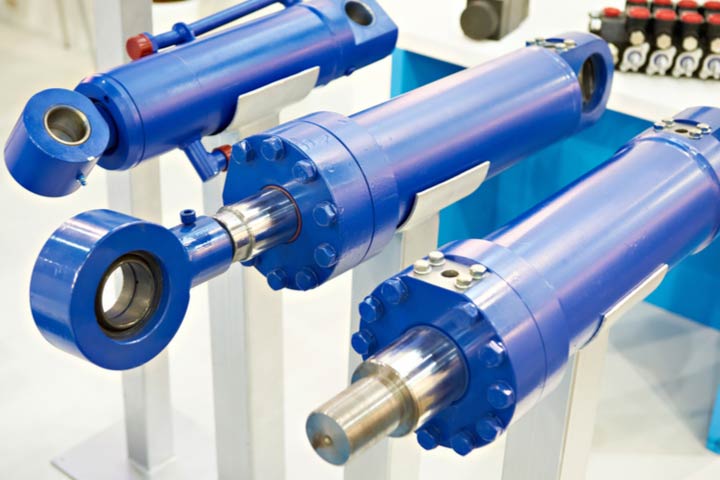
- Gears
- Bearings
- Bushings
- Sprockets
- Hydraulic cylinders
Conclusion:
In conclusion, semi-centrifugal casting is a versatile manufacturing process and a valuable alternative to traditional casting methods. It is particularly chosen for producing high-quality, dense castings of symmetrical shapes. However, you need to consider the process limitations and weigh them against the potential benefits before choosing this method.
How TOPGRID can help you ?
We TOPGRID, your manufacturing partner, offer you 50+ such manufacturing processes. You can choose as per your product needs.
We’re dedicated to upholding the highest standards of quality throughout every stage of your manufacturing process.
From the initial design to the final product completion, we assure you that the materials that undergo these processes and the products produced are quality-checked.
You can completely rely on Us! We simplify your complicated manufacturing processes!
Topgrid – Centrifugal Casting Services
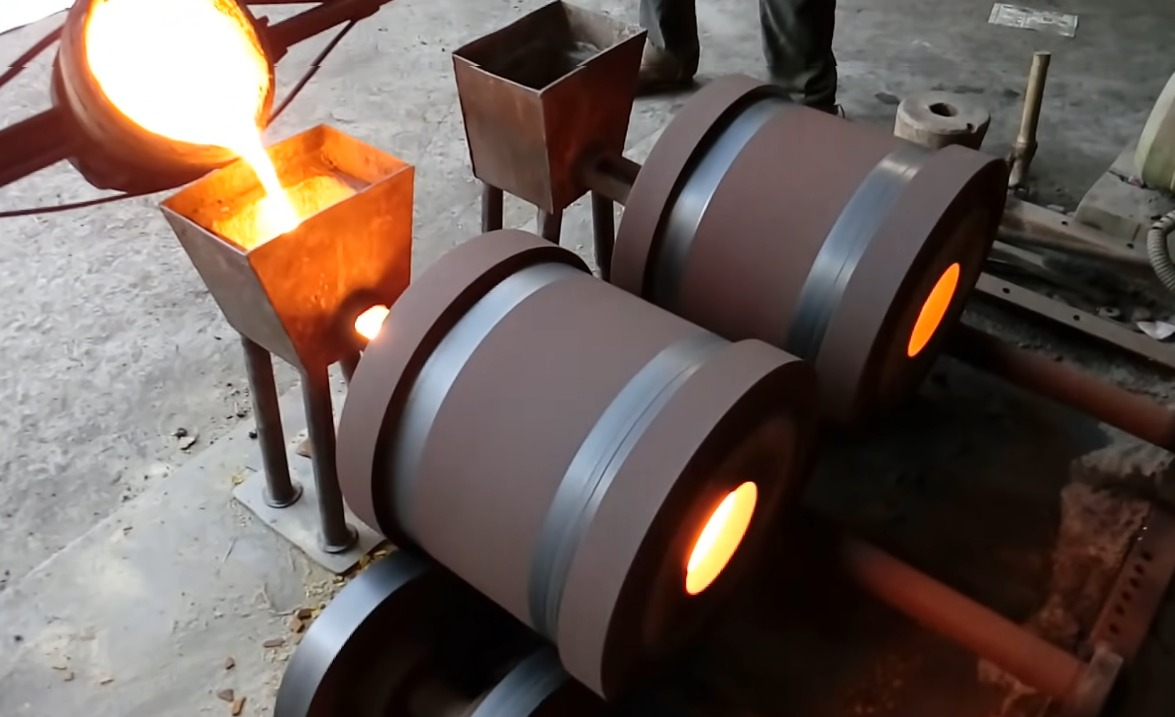
- At Topgrid, we pride ourselves on being a best provider of Centrifugal Casting Services.
- Topgrid’s Centrifugal casting services are ideal for a wide range of industries, including automotive, aerospace, electronics, medical, and consumer goods.
- If you are looking for a high-quality, reliable Centrifugal provider, contact Topgrid today.