Extrusion Blow Molding (EBM) is a specific type of blow molding. It is the most commonly employed blow molding process.
The extrusion blow molding process is commonly used for manufacturing items like bottles, containers, and automotive components.
In this article, let’s see,
- What is Extrusion Blow Molding (EBM)?
- Extrusion Blow Molding (EBM) Process
- Types of Extrusion Blow Molding (EBM)
- Extrusion Blow Molding Machines
- Advantages of Extrusion Blow Molding (EBM)
- Disadvantages of Extrusion Blow Molding (EBM)
What is Extrusion Blow Molding (EBM) ?
The extrusion blow molding process involves continuously extruding a molten plastic tube, also known as parison. It is then captured in a mold and inflated with air to take the shape of the mold. This results in the formation of hollow plastic objects.
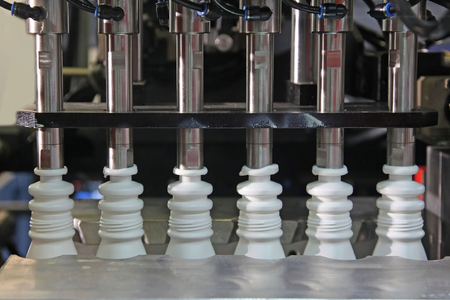
This process is widely utilized for the production of items like bottles and containers.
Extrusion blow molding (EBM) is a specific process within the broader category of blow molding.
To learn more about Blow Molding, check out our blog, Blow Molding
Extrusion Blow Molding (EBM) Process
If your products need an extrusion blow molding manufacturing process, you need to know its step-by-step work process. This enables you to have efficient communication with your production teams.
Here is an overview of the work process of extrusion blow molding.
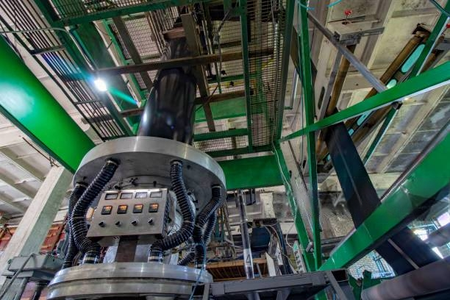
Step:1
A plastic resin, in pellet form, is fed into an extruder. Then it gets melted. The molten plastic is forced through a die, creating a continuous hollow tube. This plastic tube is commonly known as a parison. It is typically extruded vertically downwards.
Step:2
The step:2 involves, parison clamping. The mold is usually made of metal or plastic. The parison is then captured between two halves of the mold. The two halves of the mold are clamped together to hold the parison in place.
Step:3
The mold closes, and a nozzle extends into the parison. Compressed air is then injected into the parison. The air pressure causes the parison to expand and forces it to take the shape of the mold.
The air pressure must be in control to avoid the parison from bursting.
Step:4
The plastic cools and solidifies in the mold cavity. It may take only a few seconds. The cooling time is also controlled to ensure that the plastic does not shrink or warp.
Step:5
The mold opens and the newly formed hollow plastic object is ejected from the mold. The part is then trimmed to remove any excess material.
Extrusion blow molding is a continuous process. The steps above are repeated continuously to produce a continuous stream of parts.
Types of Extrusion Blow Molding (EBM)
The two major types of extrusion blow molding are,
- Continuous Extrusion Blow Molding
- Intermittent Extrusion Blow Molding
Continuous Extrusion Blow Molding
- Generates a continuous, uniform hollow tube of plastic called a parison. The parison is then captured by a mold, and air is blown into it to expand and get the mold shape. Thus creating the final product.
- It operates without interruption. Hence suitable for high-volume production.
- Continuous Extrusion Blow molding is well-suited for automated processes due to its continuous nature.
- This process results in a consistent cross-sectional shape throughout the production.
Intermittent Extrusion Blow Molding
- Intermittent Extrusion Blow Molding involves periodic extrusion of the parison, allowing for more shape control.
- The process gets paused between parison extrusions. This provides flexibility for custom designs.
- The Intermittent Extrusion Blow Molding process is well-suited for products with intricate designs or variations in thickness.
- In this process, it is easier to implement changes in mold or tooling between parison extrusions.
Thus when it comes to high-volume and standardized production you can choose the continuous extrusion blow molding process. And when it comes to flexibility for customized designs and shapes, you can go for the intermittent extrusion blow molding process.
Note: Always consult with a manufacturing specialist or expert to determine the most suitable process for your specific application.
Extrusion Blow Molding Machines
There are two commonly used extrusion blow molding machines.
They are,
- Continuous extrusion blow molding machine
- Accumulator extrusion blow molding machine
Continuous extrusion blow molding machine
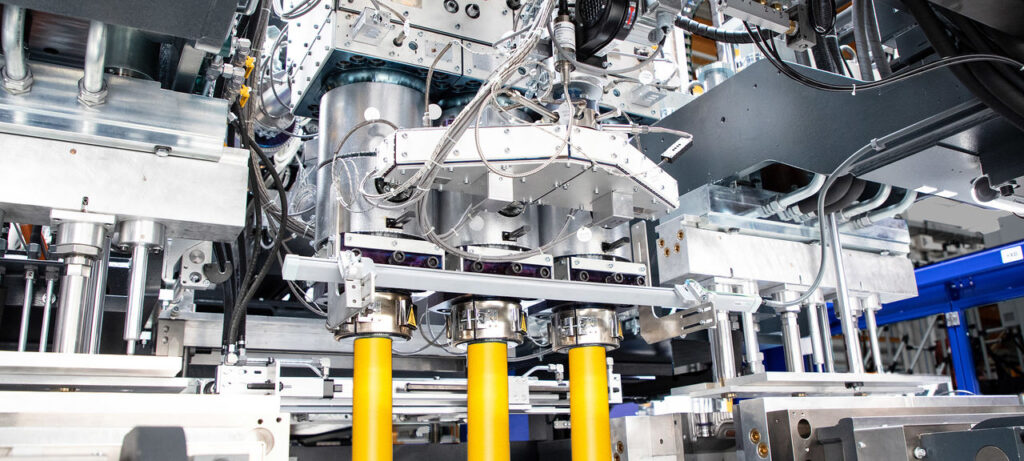
- This is the most commonly used extrusion blow molding machine.
- It is characterized by the continuous extrusion blow molding process.
- Continuous extrusion blow molding machines can produce a continuous stream of parts, resulting in high production rates and cost-effectiveness.
- Continuous extrusion blow molding machines are widely used in various industries to produce a vast array of hollow plastic products, including,
1. Bottles and containers
2. Toys and playground equipment
3. Automotive components
4. Industrial products
- Routine maintenance and inspection of the machine are crucial to ensure its safe operation and prevent malfunctions that could lead to accidents.
With its wide range of applications and adherence to safety standards, the continuous extrusion blow molding machine remains a valuable tool in various industries!
Accumulator extrusion blow molding machine
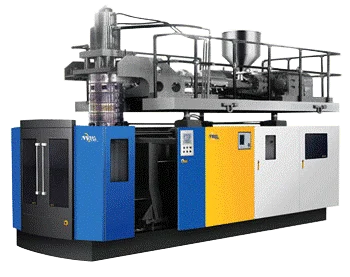
- An accumulator extrusion blow molding machine is a type of extrusion blow molding machine that uses an accumulator to store molten plastic before it is extruded into a parison.
- This machine is generally used for materials with low melt strength or for producing parts with long cycle times.
- Accumulator extrusion blow molding machine has the advantage of better control of parison thickness. The accumulator head can precisely control the amount of plastic that is transferred to the parison. This results in more consistent parison thickness.
- Accumulator extrusion blow molding machines are typically more expensive than continuous extrusion blow molding machines.
- It is used in the manufacturing of a wide variety of products, including bottles, containers, and various industrial parts.
- Regularly check and clean the accumulator, die, and mold to prevent material buildup and ensure optimal performance.
In summary, accumulator extrusion blow molding machines are a versatile and efficient way to produce large, hollow plastic parts. Thus these are the two major types of extrusion blow molding machines.
You can select the one based on production volume, product size, budget constraints, and customization needs. This helps you in getting optimal efficiency in your specific manufacturing requirements.
Advantages of Extrusion Blow Molding (EBM)
The extrusion blow molding process offers several advantages, they are,
- Extrusion blow molding is more economical for large-scale production of hollow plastic products.
- Allows for the production of a wide range of shapes and sizes, accommodating diverse packaging needs.
- Well suited for creating lightweight yet durable containers. Hence contributing to cost-effective transportation and reduced material usage.
- The molds are made using aluminum. Hence the molds used in this method are inexpensive compared to other manufacturing methods.
Disadvantages of Extrusion Blow Molding (EBM)
The extrusion blow molding process has limitations too. They are as follows.
- Since the parison is stretched too thin, filling the corners may be difficult.
- The process may generate more material waste compared to other molding methods, affecting the overall efficiency.
- There will always be a need for secondary operations like removing flash, putting holes, and other features. These can be done only after removing the part from the mold.
- Production cycle time can be longer, especially for intricate designs, impacting the overall production speed.
Conclusion
In conclusion, while extrusion blow molding offers several advantages, it comes with certain limitations. Despite limitations, it remains a valuable choice in various manufacturing units.
Understanding the specific requirements of your project and consulting the manufacturing specialist or experts are crucial for determining whether extrusion blow molding is the suitable method.
How TOPGRID can help you ?
We TOPGRID, your manufacturing partner, offer you 50+ such manufacturing processes. You can choose as per your product needs. We’re dedicated to upholding the highest standards of quality throughout every stage of your manufacturing process.
From the initial design to the final product completion, we assure you that the materials that undergo these processes and the products produced are quality-checked.
You can completely rely on Us! We simplify your complicated manufacturing processes!
Topgrid – Blow Molding Service
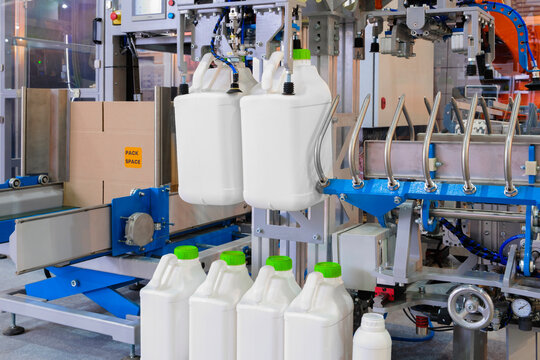
- At Topgrid, we pride ourselves on being a best provider of Blow Molding Services.
- With a strong commitment to precision, innovation, and customer satisfaction, we are your trusted partner for all your plastic injection molding needs.