Gravity die casting plays a vital role in various industries, shaping the world around us. From the cars we drive to the electronic devices we use every day, this gravity die casting process contributes to the creation of essential components that power our modern lives.
Gravity die casting process, despite its seeming simplicity, involves meticulous planning, accurate execution, and a deep understanding of materials and thermodynamics.
Let’s explore further, This article will give you insight into,
- What is Gravity Die Casting (GDC)?
- Gravity Die Casting (GDC) Process
- Materials used in Gravity Die Casting (GDC)
- Aluminum Gravity Die Casting
- Applications of Gravity Die Casting (GDC)
- Advantages of Gravity Die Casting (GDC)
- Disadvantages of Gravity Die Casting (GDC)
- Gravity Die Casting (GDC) – Defects and Remedies
- How TOPGRID can help you ?
What is Gravity Die Casting (GDC) ?
Gravity die casting (GDC) is a metal casting process. In this process, the molten metal is poured into a reusable mold using the force of gravity. The mold is typically made of metal and is preheated.
This is the definition of Gravity die casting (GDC).
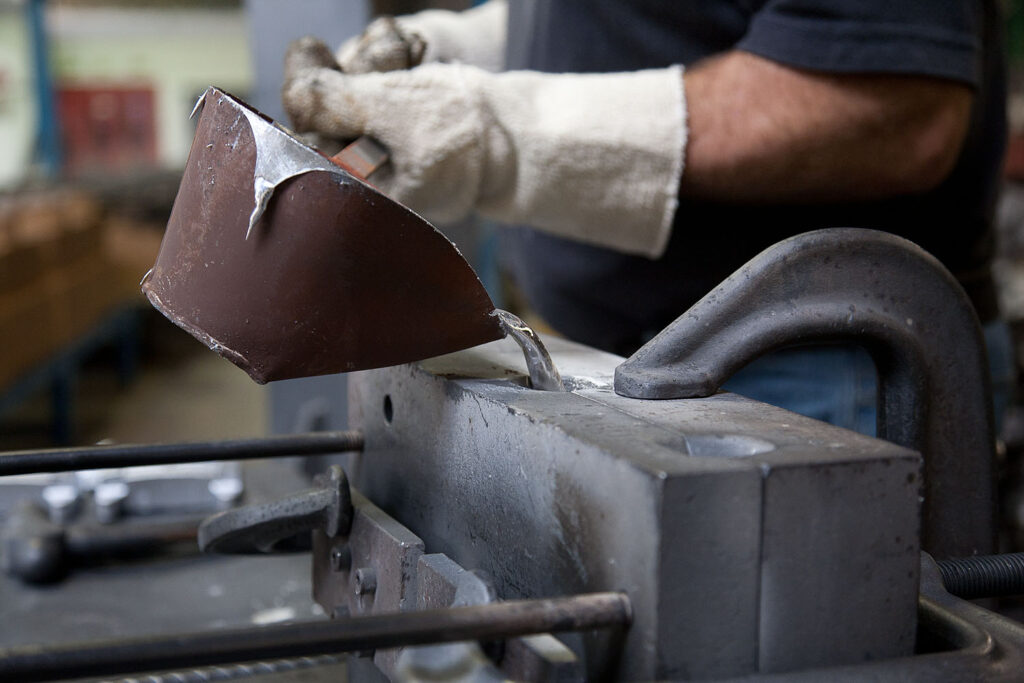
The gravity die casting process offers several advantages, making it a popular choice for producing high-quality metal components.
Next, we must learn about the step-by-step process of gravity die casting. This helps you in having efficient communication with your production teams and helps in handling problems that arise in your production.
Here follow the gravity die casting process steps in detail.
Gravity Die Casting (GDC) Process
The step-by-step work process of the gravity die casting process is,
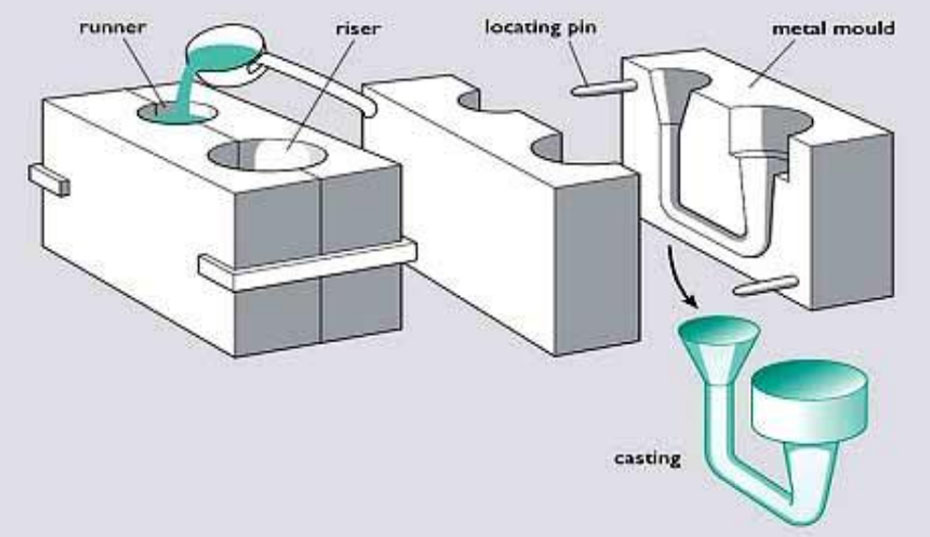
Step:1
The gravity die casting process starts with developing a reusable metal pattern. The metal pattern is typically made from aluminum or steel, representing the final product.
Step:2
The pattern is placed into a two-part metal mold, creating a cavity that matches the desired shape of the product.
Step:3
The chosen metal is melted in a furnace to a specific temperature, ensuring proper fluidity.
Step:4
A refractory coating is applied to the mold’s interior surfaces. This helps to enhance heat resistance and facilitate metal flow. The mold is closed, securing both halves together. This creates a sealed cavity ready for casting.
Step:5
The mold is positioned vertically. Then the molten metal is poured into the mold’s inlet. Gravity force facilitates the metal’s flow into the mold cavity. Gravity draws the metal down, filling the cavity.
Step:6
The metal cools and solidifies within the die, taking the shape of the pattern. The cooling time varies depending on the part size and metal used.
Step:7
After the metal solidifies, the mold is opened. The finished part is ejected. The mold can be reused for subsequent castings.
Step: 8
Excess materials such as gates and risers are removed. If necessary post-casting operations are performed to achieve the final product specifications. Thus these are the steps involved in the gravity die casting process.
The process is repeated for additional castings, using the same mold. The same mold can be reused until it shows signs of wear or deterioration.
Materials used in Gravity Die Casting (GDC)
In the gravity die casting process, the mold material needs to withstand the repeated heating and cooling cycles. The casting materials should meet the mechanical and functional requirements of the end product.
The primary materials used in gravity die casting involve:
Mold materials: Aluminum, Steel, Copper.
Refractory Coating: Zircon.
Release Agents: Graphite-Based Lubricants.
Core Pins and Inserts: Tool Steel or Stainless Steel.
Casting Alloys: Aluminum Alloys, Zinc Alloys, Copper Alloys.
The choice of materials depends on factors such as the desired properties of your final product, your production volume, and the cost considerations of your specific projects.
Note: Always consult with a materials engineer or a manufacturing specialist to determine the most suitable materials for your specific application.
Aluminium Gravity Die Casting
Aluminium gravity die casting is a specific type of gravity die casting. It is the most commonly employed gravity die casting method. It is used to create intricate and high-quality aluminium components.
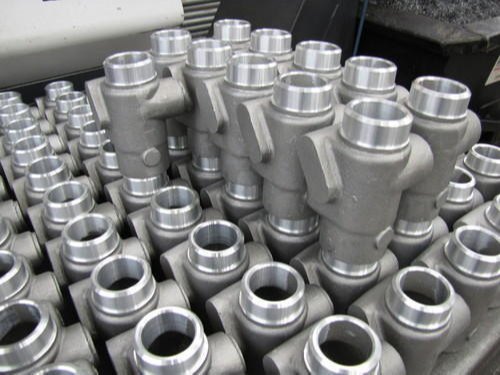
Gravity die casting involves pouring molten metal into a metallic mold using the force of gravity. While in aluminium gravity die casting, the metal being cast is specifically aluminium.
That is, in aluminium gravity die casting method, molten aluminium is poured into a metallic die. The metallic die is generally made of steel. Then gravity draws the molten aluminium down, filling the die cavity completely.
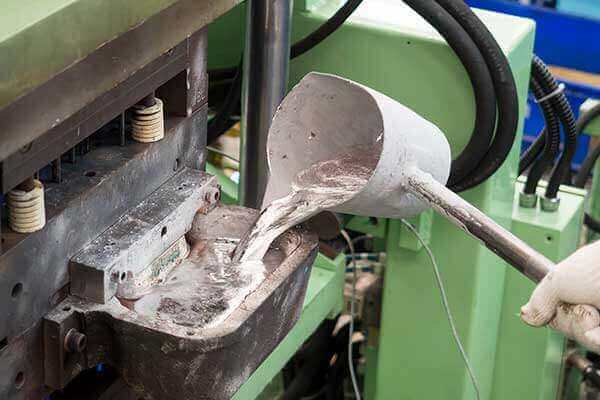
Aluminium gravity die casting process is widely used in automotive, aerospace, and various industrial applications. It can deliver precise and durable aluminium parts at a relatively low cost.
Applications of Gravity Die Casting (GDC)
Gravity die casting can produce high-quality parts with excellent dimensional accuracy, surface finish, and mechanical properties. Hence it is used to manufacture various products across various industries.
A few applications of Gravity die casting are,
Automotive Components:
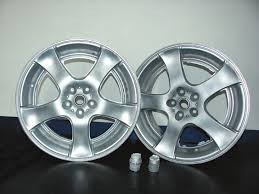
- Wheels
- Engine blocks
- Brake calipers
- Cylinder heads
- Intake manifolds
- Transmission cases
- Transmission covers
Aerospace Components:
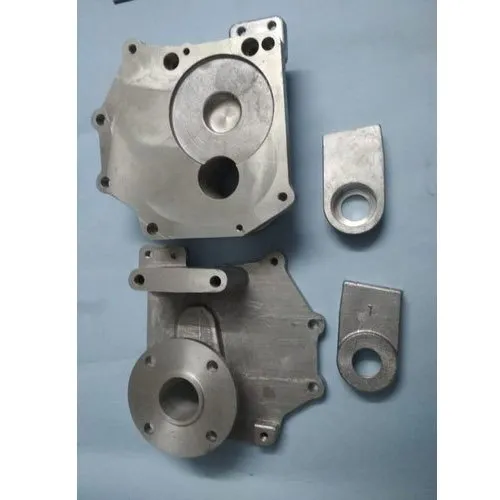
- Engine parts
- Structural components
- Fuel system components
Industrial Components:
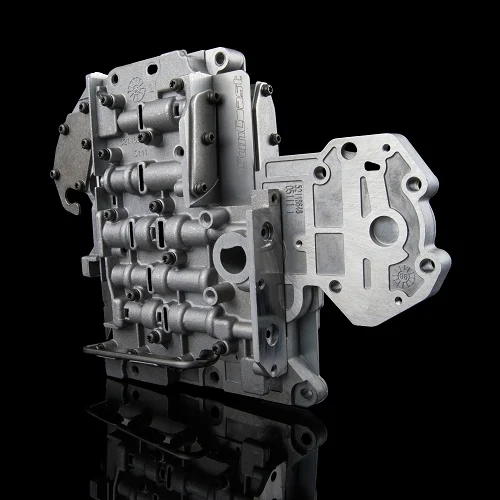
- Valves
- Impellers
- Pump housings
- Electrical enclosures
Medical Industries:
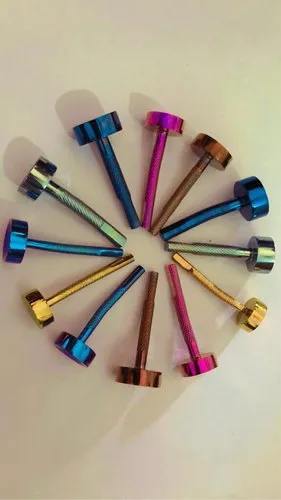
- Screws
- Forceps
- Scalpels
- Hemostats
- Bone plates
- Orthopedic implants
- Housings for medical devices
- Components for diagnostic equipment
Consumer Goods:
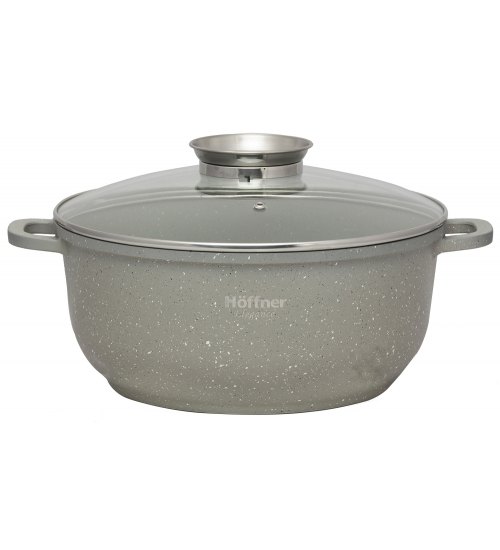
- Cookware
- Kitchenwares
- Lighting fixture
- Decorative accents.
Sporting Goods:
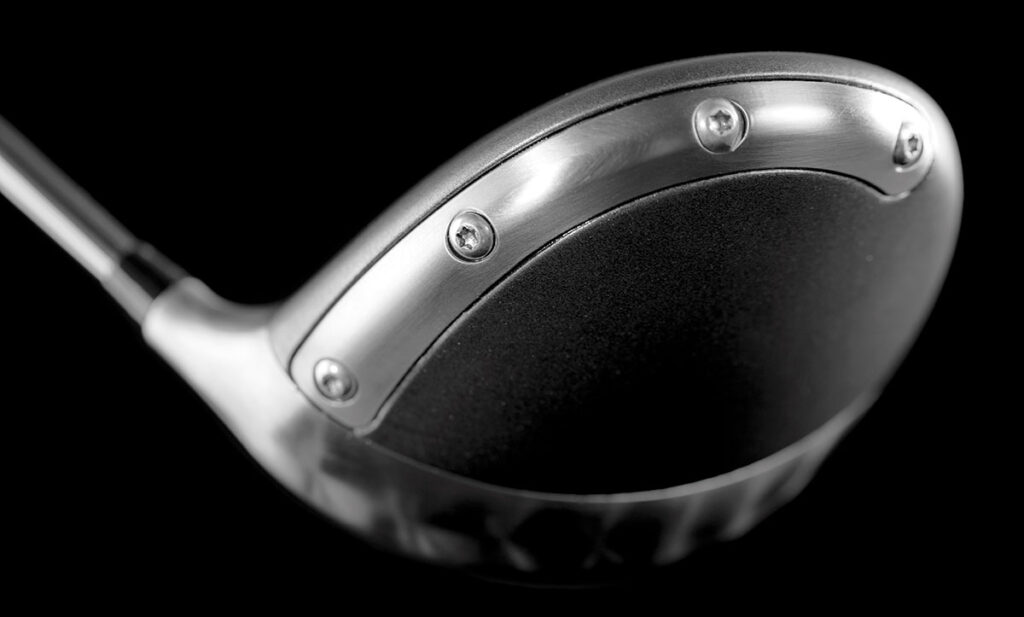
- Golf clubs
- Fishing rods
- Bicycle components
In summary,
Gravity die casting is a versatile and efficient metal casing process. Hence plays a crucial role across various industries for various applications. When it comes to employing a manufacturing process, you must be aware of both its pros and cons.
Like any manufacturing process, gravity casting comes with its own set of advantages and disadvantages. Let’s see both, this will help you determine if it’s the right fit for your needs.
Advantages of Gravity Die Casting (GDC)
The gravity die casting process offers several advantages, they are,
- Gravity casting produces parts with exceptional dimensional accuracy, smooth surfaces, and good mechanical properties. This makes it ideal for producing intricate components.
- While the initial die setup can be expensive, it’s reusable for thousands of casting. Thus it is cost-effective for medium-volume production.
- Compared to other casting methods, gravity casting generates less scrap metal. Thus minimizing waste and environmental impact.
- Aluminium, zinc, copper, and magnesium alloys are all compatible with this process.
- The relatively simple work process allows for quicker production cycles.
Disadvantages of Gravity Die Casting (GDC)
The gravity die casting process has disadvantages too which must be taken into consideration before deciding to employ this process for your project. The disadvantages are,
- Gravity die casting typically works best for parts smaller than 100 pounds. Because larger pieces can deform the mold under molten metal weight.
- In gravity die casting, draft angles need to be incorporated into the part design to facilitate easy ejection from the die. This limits design freedom in some cases.
- Metals with high melting points or requiring pressurization for intricate details might not be suitable for gravity casting.
- Rapid cooling can lead to small air pockets within the casting. Hence may need additional machining depending on the application.
- Setting up the initial die can take several weeks. Therefore it is less suitable for projects requiring immediate production.
Gravity Die Casting (GDC) – Defects and Remedies
Some problems may arise while you’re doing gravity die casting. These problems or defects can be rectified or controlled using the following remedies.
1. Air pockets: Tiny bubbles get trapped inside the part.
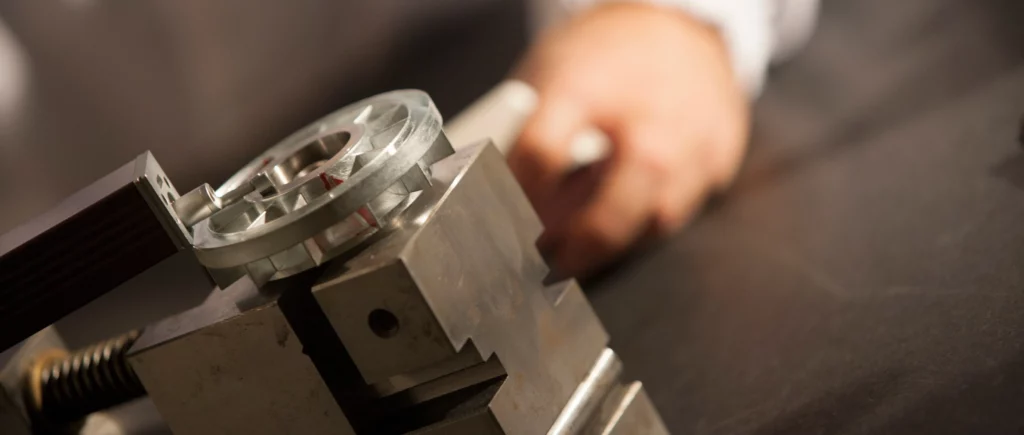
Remedy: You must slow down the cooling process. Use chills or risers to direct heat flow, and maybe add some special melting techniques.
2. Wrinkles (cold shuts): Metal didn’t flow fast enough, leaving behind unwanted creases and folds.
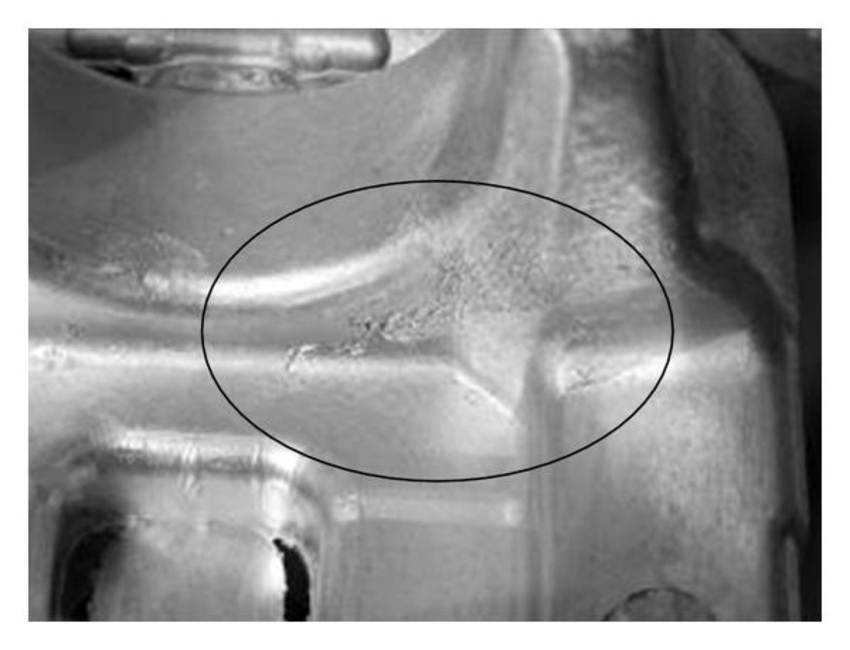
Remedy: Crank up the temperature, both metal and mold. And you must adjust the pouring speed or gate design to get that smooth flow.
3. Blisters: Trapped gas pockets making your part look like it has bubble wrap on the inside.
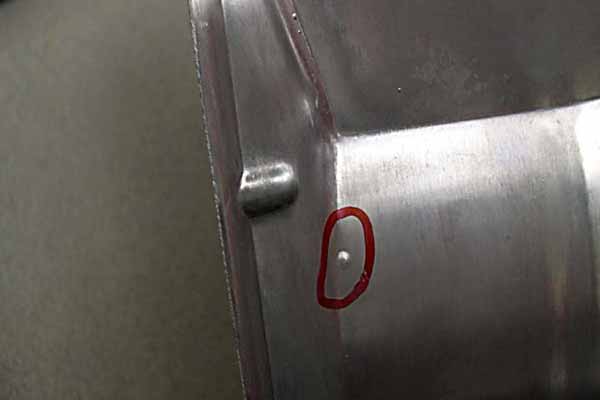
Remedy: You must degas the metal, using the right pouring technique, and optimize the mold venting. This helps those pesky gas bubbles escape.
4. Cracks: Not the kind you want in your parts, more like tiny fractures or splits.
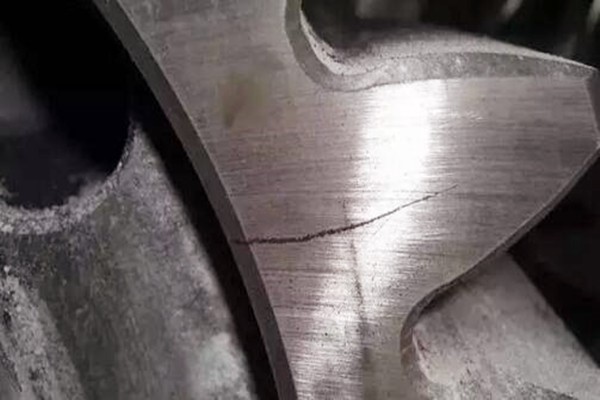
Remedy: To solve this you must be gentle with the cooling process and avoid stress concentrations in the design. Also, you must choose the right metal alloy for the job
5. Incomplete casting: Didn’t quite fill the mold, leaving you with a part missing a chunk.
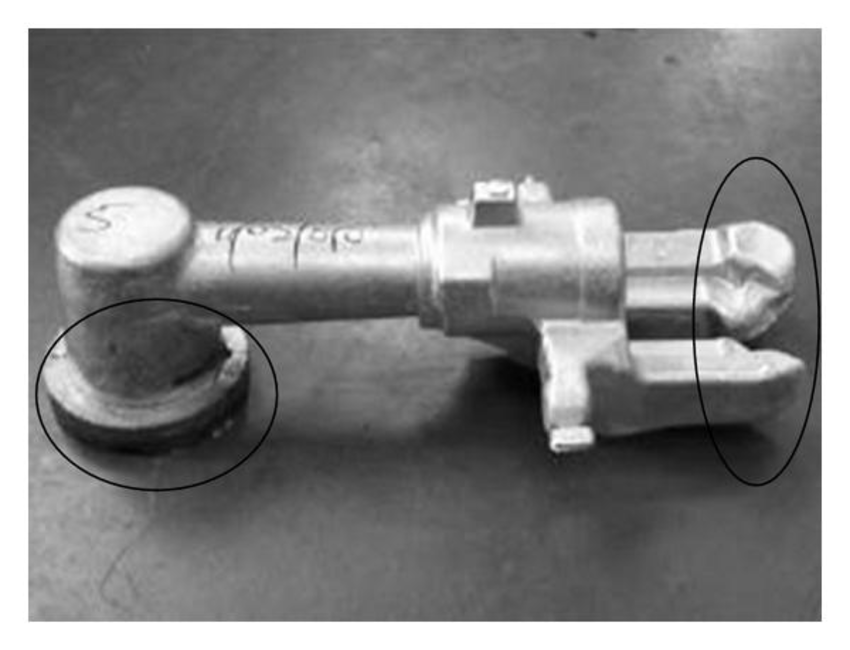
Remedy: You must make sure the mold is properly vented and adjust the pouring parameters. And, consider using risers or chills to improve metal flow.
In summary,
When gravity casting, you must remember these two key things, control the flow and tame the heat. Master these and gravity die casting will be your superpower!
Note:
Various processing changes are suggested as possible solutions or remedies for the different problems encountered during the gravity die casting process. In general, these changes should not exceed the recommended ranges. Consult officials or executives for the right range to be employed.
At TOPGRID, 760+ consultants are available to assist you in troubleshooting the problems.
Conclusion
Gravity die casting, with its molten metal filling molds, is a marvel of engineering. Gravity die casting is not just about metal, it’s about shaping the world around us. So, if you’re considering this technique, approach it with the required knowledge and information.
How TOPGRID can help you ?
We TOPGRID, your manufacturing partner, offer you 50+ such manufacturing processes. You can choose as per your product needs. We’re dedicated to upholding the highest standards of quality throughout every stage of your manufacturing process.
From the initial design to the final product completion, we assure you that the materials that undergo these processes and the products produced are quality-checked.
You can completely rely on Us! We simplify your complicated manufacturing processes!
Topgrid – Gravity Die Casting Services
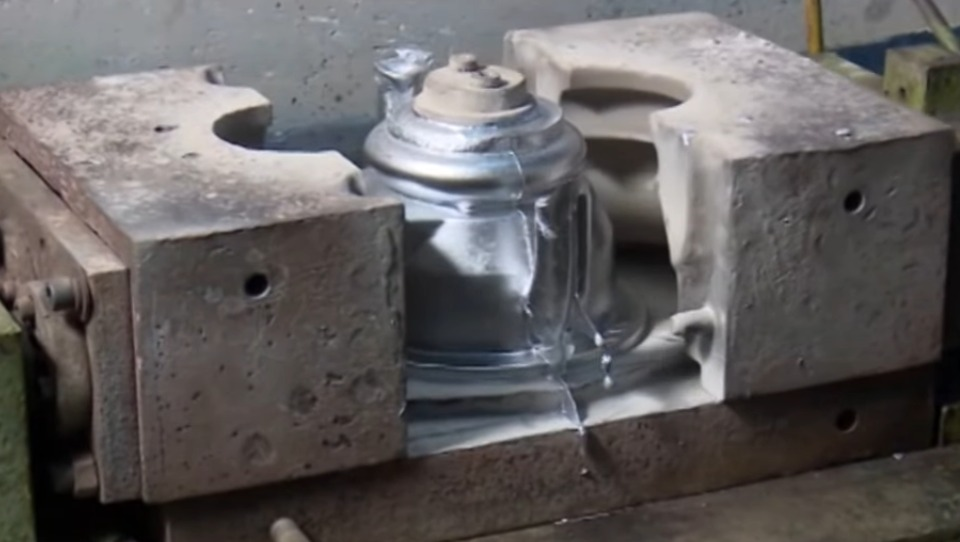
- At Topgrid, we pride ourselves on being a best provider of Gravity Die Casting Services.
- With a strong commitment to precision, innovation, and customer satisfaction, we are your trusted partner for all your Gravity Die Casting Services needs.