High-pressure die casting (HPDC) is a manufacturing process that involves injecting molten metal into a steel mold die under high pressure. This forces the metal to take the shape of the die cavity.
High-pressure die casting is an efficient process that can be used to produce a wide variety of parts, from small, intricate components like surgical tools in medical industries to large complex vehicle parts.
This article will give you insights into,
- What is High Pressure Die Casting (HPDC) ?
- High Pressure Die Casting (HPDC) Process:
- Advantages and Disadvantages of High Pressure Die Casting:
- Disadvantages of High Pressure Die Casting:
- Applications of High Pressure Die Casting:
- How TOPGRID can help you ?
What is High Pressure Die Casting (HPDC) ?
High-pressure die casting is a metal casting process that involves forcing molten metal under high pressure into a mold cavity. The mold cavity is typically made of steel. The mold cavity is created by two halves of a die.
The molten metal is injected into the die cavity at high pressure. The pressure typically ranges from 100 to 1000 Mpa. This forces the metal to conform to the shape of the die cavity, resulting in precision casting.
Next, we must learn about the step-by-step process of High-pressure die casting. This benefits you in having efficient communication with your production teams and helps in handling problems that arise in your production.
Here follow the high pressure die casting process steps in detail.
High Pressure Die Casting (HPDC) Process
The step-by-step process of high-pressure die casting is as follows:
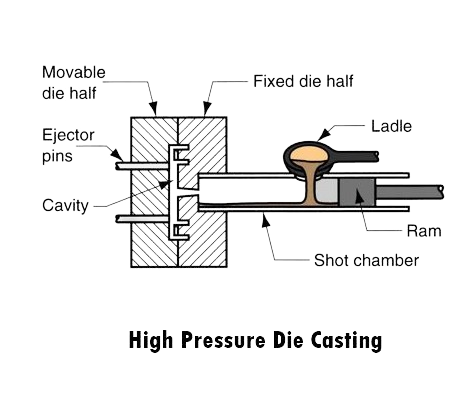
Step:1
Die Preparation:
The die is cleaned and inspected. This helps you to ensure that it is free of defects and that the surfaces are smooth. The die is then preheated to the appropriate temperature to ensure proper metal flow and solidification.
Step:2
Injection:
Molten metal is poured into a shot sleeve (shot chamber). The shot sleeve is a heated chamber that is connected to the die cavity. The plunger in the shot sleeve is then forced forward, injecting the molten metal into the die cavity under high pressure.
Step:3
Solidification:
Due to the high pressure applied, the molten metal comes into contact with the cool die cavity. This solidifies the metal rapidly.
Step:4
Ejection:
Once the casting has solidified, the die is opened. The final casting part is ejected. The casting is then trimmed and inspected to ensure that it meets the required specifications.
Thus these are the steps involved in the high pressure die casting process. If you’re looking for more die casting, you may check out our Gravity Die Casting.
Advantages and Disadvantages of High Pressure Die Casting
When choosing or learning about manufacturing processes you need to consider both the advantages and disadvantages of it. That helps you in better decision making, minimizing costs, and ensuring the quality of your products.
Here are a few advantages and disadvantages of the high-pressure die casting process.
Advantages of high pressure die casting
A few advantages of the high-pressure die casting process are,
- High-pressure die casting can produce parts at a rapid pace. This makes it suitable for high-volume manufacturing.
- High-pressure die casting delivers casting with high dimensional accuracy. This reduces the need for extensive post-processing.
- HPDC produces casting with a smooth surface finish. This minimizes the need for additional finishing steps.
- HPDC castings are known for their strength-to-weight ratio, making them ideal for various applications.
- It can be used with a wide range of metals, including aluminum, zinc, and magnesium.
- High-pressure die casting is highly responsive to automation. This enhances the production efficiency.
Disadvantages of High Pressure Die Casting
A few disadvantages of the high-pressure die casting process are,
- The initial investment in dies and equipment can be high. This makes HPDC less suitable for low-volume production.
- The rapid solidification process can lead to tiny air pockets or voids in the casting. This affects its strength and properties.
- The size and complexity of parts are restricted by the die size and design.
- Sometimes high injection pressure and rapid cooling can induce stress in the casting. This increases the risk of cracking.
- The high-pressure die casting process involves molten metal, high pressure, and potential fumes, requiring strict safety precautions and training.
Applications of High Pressure Die Casting
High-pressure die casting (HPDC) is a versatile manufacturing process that can produce a wide variety of high-quality castings.
It can produce components that require a high strength-to-weight ratio, lightweight, and dimensional accuracy. This makes it suitable for various applications in various industries including, automotive, electronics, aerospace, and consumer goods.
They are as follows.
Automotive Industry:
HPDC is used for manufacturing engine components such as,
- Engine blocks
- Cylinder heads
- Intake manifolds
- Transmission housings
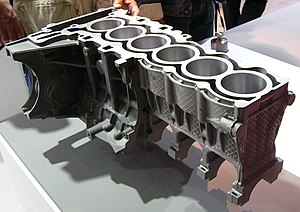
And, it is also used to manufacture structural components such as
- Wheels
- Car frames
- Suspension components
Electronic Industry:
High-pressure die casting is used to produce heat sinks for electronic components, such as
- Power transistors
- Integrated circuits
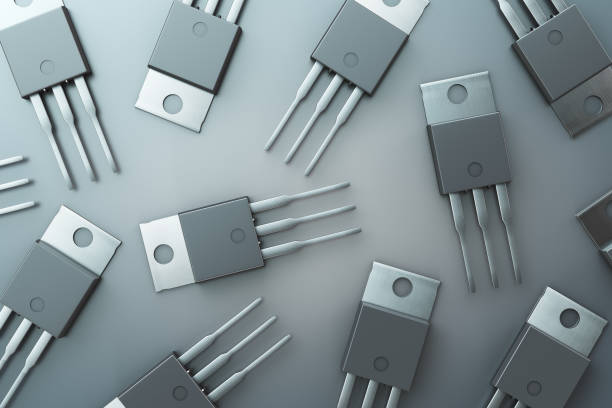
HPDC is also used to manufacture housing for electronic devices. Such as
- TVs
- Computers
- Mobile phones.
Aerospace Industry:
The High-pressure die casting process is used to produce aircraft structures such as
- Wing spars
- Fuselage components
- Landing gear components
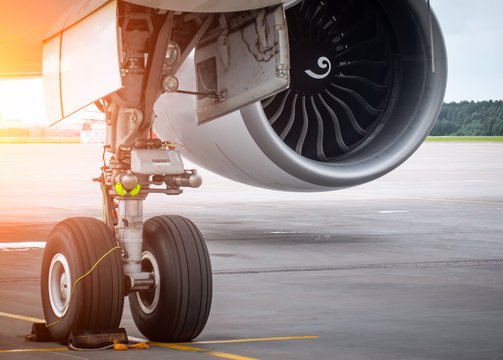
It is also used to produce fuel tanks for aircraft.
Consumer Goods Industry:
High-pressure die casting is used to manufacture appliances such as,
- Washing machines
- Refrigerators
- Dryers
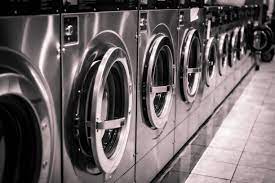
HPDC is also used to produce power tools such as
- Drills
- Saws
- Sanders

It is also used to manufacture sporting goods such as
- Golf clubs
- Baseball bats
- Hockey sticks
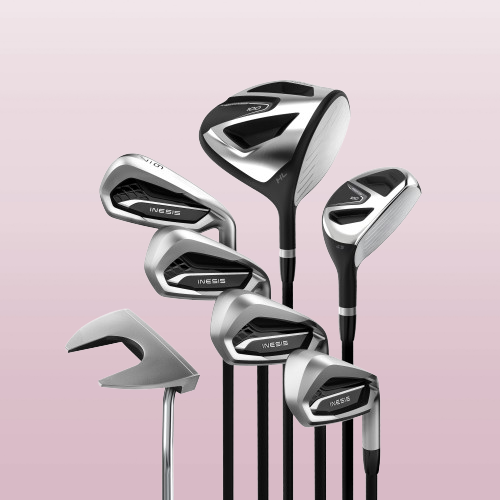
Thus the versatility, speed, and precision of high-pressure die casting make it a preferred choice for producing a wide range of complex metal components across various industries.
If you’re considering using this method for your next project, be sure to contact a manufacturing consultant to discuss your specific needs.
Conclusion:
High-pressure die casting (HDPC) plays a vital role in manufacturing products across diverse industries. Its ability to produce intricate, lightweight, high-precision metal components at high volumes makes it a preferred choice for various applications.
Understanding the specific requirements of your project and consulting the manufacturing specialist or experts are crucial for determining whether this process is a suitable method.
How TOPGRID can help you ?
We TOPGRID, your manufacturing partner, offer you 50+ such manufacturing processes. You can choose as per your product needs.
We’re dedicated to upholding the highest standards of quality throughout every stage of your manufacturing process. From the initial design to the final product completion, we assure you that the materials that undergo these processes and the products produced are quality-checked.
You can completely rely on Us! We simplify your complicated manufacturing processes!
Topgrid – High Pressure Die Casting Services
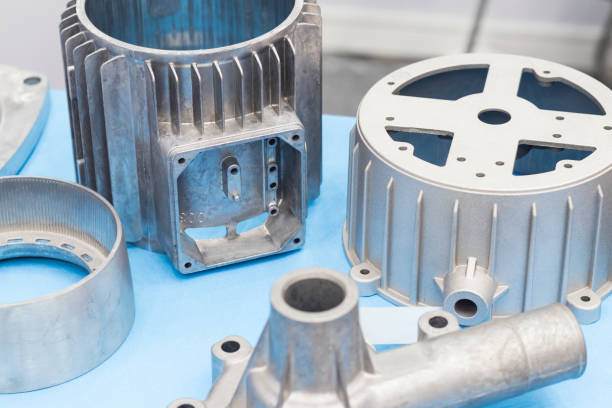
- At Topgrid, we pride ourselves on being a best provider of High Pressure Die Casting Services.
- Topgrid’s high pressure die casting services are ideal for a wide range of industries, including automotive, aerospace, electronics, medical, and consumer goods.
- If you are looking for a high-quality, reliable HPDC provider, contact Topgrid today.