Injection blow molding is a specific type of blow molding process. It is a two-stage process that combines the principles of injection molding and blow molding.
The injection blow molding process is used for manufacturing hollow objects such as bottles, jars, and containers.
In this article, we’ll see,
- What is Injection Blow Molding?
- Injection Blow Molding Process
- Injection Blow Molding Machines
- Injection Blow Molding Products and Applications
- Advantages and Disadvantages of Injection Blow Molding
- Conclusion
- How TOPGRID can help you ?
What is Injection Blow Molding ?
Injection blow molding is a manufacturing process used to produce hollow plastic objects like bottles, by injecting molten plastic into a mold, cooling it, and then inflating it with air.
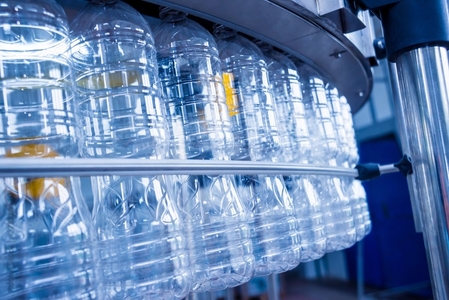
The Injection blow molding process is a specific process within the broader category of Blow Molding.
It is a similar process like the Extrusion Blow Molding process. However they differ in the way they form the initial product.
Injection Blow Molding Process
To employ the injection blow molding manufacturing process, you need to know its step-by-step work process. This enables you to have efficient communication within your manufacturing units, contributing to the efficiency and success of your business.
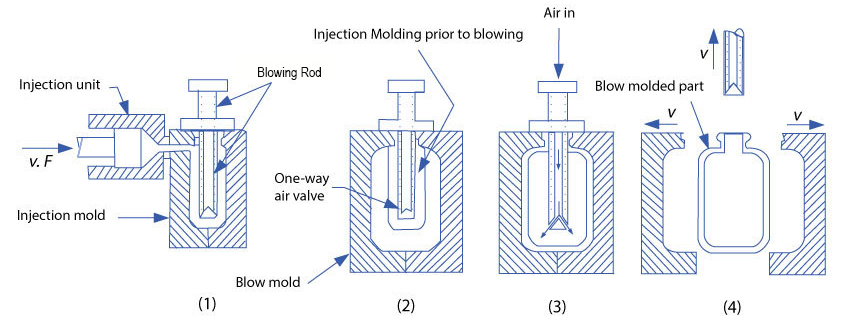
Here is an overview of the work process of injection blow molding:
Step:1
The process begins with plastic pellets. The pellets are fed into an extruder, where they are melted and liquefied by a rotating screw.
Step:2
The molten plastic is then injected into a mold cavity. There it gets rapidly cooled and solidified. This creates a preform. The preform is a hollow tube with a closed end and an open end. The preform’s shape is determined by the mold cavity, which is designed to match the final product.
Step:3
The preform is attached to a core rod. The core rod is a hollow tube that extends through the center of the preform. The core rod serves as a support for the preform. It allows air to be blown into the preform during the blow molding stage.
Step:4
The preform gets transferred to the blow molding stage. This can be done in two ways. Either by pulling the core rod through the preform or by using an indexing mechanism to move the preform from one stage to the next.
Step:5
The preform is then placed in a blow mold. The blow mold will be in the shape of the desired final product.
Step:6
Hot air is blown into the preform through the core rod. The air pressure causes the preform to expand and conform to the shape of the blow mold.
Step:7
Once the preform has taken the space of the blow mold, the air pressure is reduced. Then the mold is opened. The newly formed hollow object is cooled and ejected from the mold.
Thus these are the processes involved in injection blow molding, which involves both Injection Molding and Blow Molding.
Understanding each step of the manufacturing process helps you identify and address potential defects or inconsistencies earlier. This helps you in ensuring the production of high-quality products.
Injection Blow Molding Machines
Selecting the right machine is determined by factors like specific product requirements, production volume, and desired level of automation. By selecting the right machines you can achieve optimal production efficiency, product quality, and cost-effectiveness.
Here are a few injection blow molding machines.
Primary Types
- Vertical injection blow molding machines – used to produce smaller, thinner-walled products.
- Horizontal injection blow molding machines – used to produce larger, thicker-walled products.
Based on clamping force
- Hydraulic injection blow molding machines – use hydraulic clamping pressure and it is the most common type of injection blow molding machine.
- Electric injection blow molding machines – employ electric motors for clamping and it is more energy-efficient and environmentally friendly.
Based on the blowing system
- Single-stage injection blow molding machines – employ a single-stage blowing stage and are used for simpler product designs and offer a straightforward operation.
- Two-stage injection blow molding machines – utilize two blowing stages and are ideal for producing intricate product designs with high precision.
Note: Always consult with a manufacturing specialist or expert to determine the most suitable machine for your specific application.
Injection Blow Molding Products and Applications
The injection blow molding process is employed in various industries to manufacture several products that are regularly used. Some common injection blow molded products are as follows.
Consumer goods
- Bottles
- Jars
- Oil jugs
- Toys
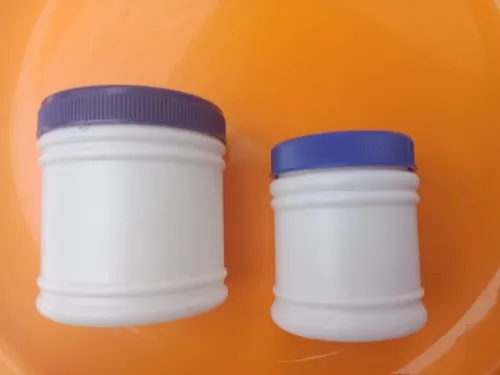
Containers
- Shampoo bottles
- Food Containers
- Cosmetic containers
- Pharmaceutical containers
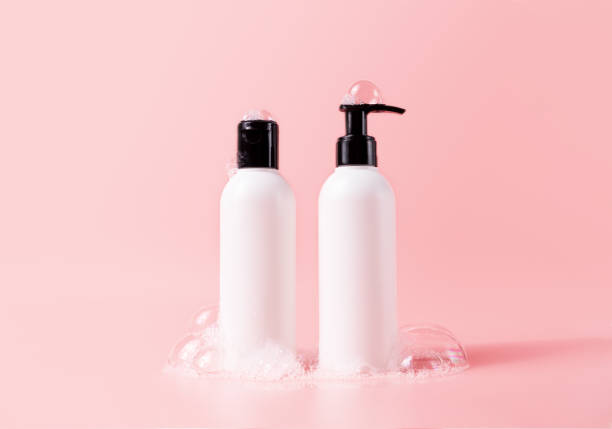
Automotive parts
- Fuel tank
- Airbags
- Headlight housings
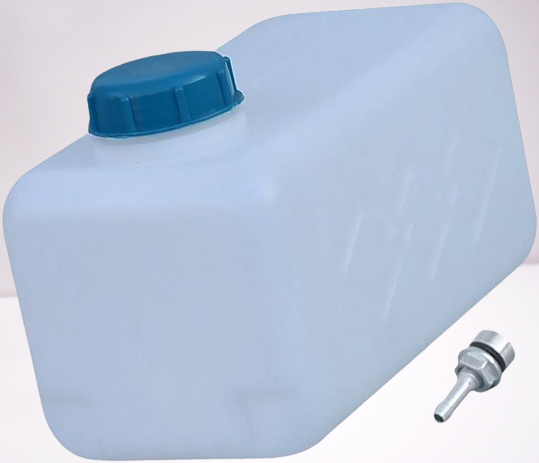
In summary, injection blow molded products are thin-walled, hollow, and plastic. Thus injection blow molding is an effective and efficient process for producing high-quality products.
Advantages and Disadvantages of Injection Blow Molding
When choosing a manufacturing process you need to consider both the benefits and limitations of it. That helps you in better-decision making, minimizing costs, and ensuring the quality of your products.
Here are a few advantages and disadvantages of the injection blow molding process.
Advantages of Injection Blow Molding Process:
- The injection blow molding process produces high-quality hollow objects with excellent dimensional accuracy and surface finish.
- It is a versatile process capable of creating a wide range of shapes and sizes.
- It has the ability to produce large quantities of products quickly.
Disadvantages of Injection Blow Molding Process:
- Injection blow molding requires a significant investment in machinery and tooling.
- It has limitations over wall thickness control. This can affect the product’s strength and performance.
- This process has slightly lower precision compared to other molding methods, such as Injection Molding.
Conclusion
In conclusion, injection blow molding is a versatile manufacturing process widely used in the production of plastic containers. Its unique combination of injection molding and blow molding techniques allows for the creation of complex and precise hollow objects with excellent consistency.
Understanding the specific requirements of your project and consulting the manufacturing specialist or experts are crucial for determining whether injection blow molding is a suitable method.
How TOPGRID can help you ?
We TOPGRID, your manufacturing partner, offer you 50+ such manufacturing processes. You can choose as per your product needs. We’re dedicated to upholding the highest standards of quality throughout every stage of your manufacturing process.
From the initial design to the final product completion, we assure you that the materials that undergo these processes and the products produced are quality-checked.
You can completely rely on Us! We simplify your complicated manufacturing processes!
Topgrid – Blow Molding Service
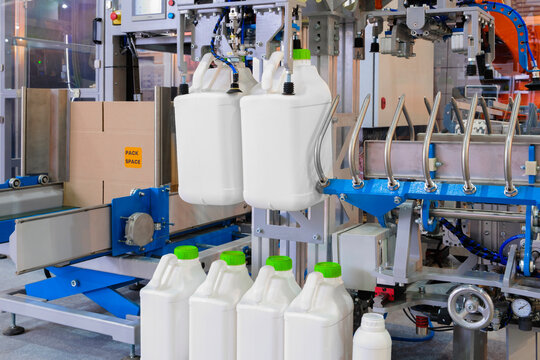
- At Topgrid, we pride ourselves on being a best provider of Blow Molding Services.
- With a strong commitment to precision, innovation, and customer satisfaction, we are your trusted partner for all your plastic injection molding needs.