Topgrid is Manufacturing service provider helps you to transform your manufacturing journey from frustration to fulfilment. So far we have worked more than 50+ project in injection molding. With those intensive knowledge, we have created this blog post which helps you better understanding about injection molding
Table of Content:
- Injection molding
- Injection Molding Process
- Topgrid approach to injection molding
- Advantages of injection molding
- Application of injection molding
- Conclusion
What is Injection Molding ?

Injection molding is a manufacturing technique used to create parts and products by injecting molten material into a mold cavity.
The material, typically thermoplastic or thermosetting plastic, is forced into the mold under high pressure and temperature conditions. After cooling and solidifying inside the mold, the final product is removed, ready for use.
Injection Molding Process
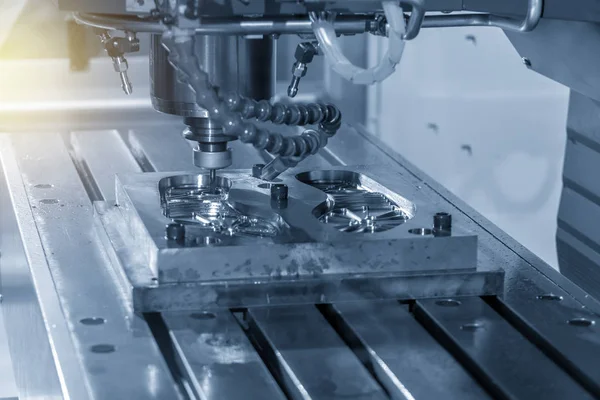
Understanding the injection molding process is crucial to grasp the intricacies of this manufacturing method. Here are the key steps involved:
Material Preparation:
The process starts with selecting the appropriate material. Common choices include polyethylene, polypropylene, and ABS due to their ability to be melted and reshaped repeatedly. These materials are usually provided in the form of pellets or granules and are loaded into the injection molding machine.
Melting:
The selected material is heated within the machine’s barrel until it reaches a molten state. Precise temperature and pressure control are essential to achieve the optimal material condition for injection.
Injection:
Once the material is molten, it is injected into the mold cavity through a runner system. The mold cavity is designed to replicate the desired part or product’s shape.
Cooling:
As the molten material fills the mold cavity, it begins to cool and solidify. Cooling is a critical phase that affects the product’s final quality and structure. Mold cooling can be expedited using cooling channels integrated into the mold.
Ejection:
After adequate cooling and solidification, the mold opens, and the finished product is ejected. Ejection pins, plates, or other mechanisms are employed to remove the product from the mold.
Post Processing:
In some cases, additional post-processing steps like trimming, painting, or assembly may be necessary to meet specific product requirements.
Topgrid approach to injection molding
Topgrid provides End to End manufacturing solution in multiple manufacturing process. We divides any injection molding project into the following phases:
Tooling Phase:
- Understand the customer needs: We understand customer needs in great detail. Here are some of the parameters that we try to understand:
- Customer industry
- Product and part type
- Precision requirement
- Aesthetic requirement
- Longevity
- Understanding the sweet balance between optimising Capex vs Opex
- Design for Manufacturability: We evaluate every aspect of the part design for manufacturability, cost implications of the decisions
- Tool Design & Mold flow analysis
- Tool Manufacturing with verification after every process
Production phase:
- Match the right manufacturing partner based on the machinery specifications, price, quality, geographical location, volume expectations of the project
- We provide Topgrid’s supply chain management solution that includes Quality checks, payment safety, vendor replacement guarantee, logistics support through our state of the art tech enabled platform to manage end to end customer needs.
This scientific approach helps our customers reduce all the unforeseen risks that are generally associated with injection molding tooling and production processes.
” Ready to Manufacture ? Tell us your Needs! “
Advantages of Injection Molding
Injection molding offers several advantages, making it a preferred manufacturing method in various industries:
Precision and Consistency: Injection molding ensures high precision and uniformity across production runs, resulting in identical parts or products.
Cost-Effective: Once the mold is created, the cost per part decreases significantly, making it cost-effective for large-scale production.
Material Variety: The process accommodates a wide range of materials, providing flexibility in material selection.
Complex Geometry: Injection molding can produce intricate shapes and complex designs that are challenging to achieve with other methods.
Reduced Waste: Minimal material wastage, and excess material can often be recycled.
Applications of Injection Molding
Injection molding finds applications across diverse industries, including:
Automotive: Interior components, dashboard parts, and under-the-hood parts.
Electronics: Housings for electronic devices, connectors, and consumer electronics casings.
Medical: Medical device components, syringe barrels, and disposable medical equipment.
Packaging: Bottles, caps, and containers for the food and beverage industry.
Toys and Consumer Goods: Plastic toys, household appliances, and consumer product packaging.
Conclusion
Injection molding is a versatile, cost-effective, and precise manufacturing process with a broad range of applications. Understanding the injection molding process and its benefits is essential for businesses looking to produce high-quality plastic components efficiently.
We hope this guide has shed light on the fascinating world of injection molding and its significance in modern manufacturing.
Topgrid is Manufacturing service provider helps you to transform your manufacturing journey from frustration to fulfilment. We provides End to End manufacturing solution in multiple manufacturing process.
” Ready to Manufacture ? Tell us your Needs! “