Reaction Injection Molding (RIM) is a manufacturing process used to produce plastic parts. The reaction injection molding process involves mixing of two liquid components and being injected into the mold. They react chemically, forming a polymer inside the mold cavity and solidifying into the desired shape.
RIM is commonly used for large and complex parts that need high-quality surface finish.
Read further if you want to know more about,
- What is Reaction Injection Molding (RIM)?
- Reaction Injection Molding (RIM) Process
- Materials used in Reaction Injection Molding (RIM)
- Advantages of Reaction Injection Molding (RIM)
- Disadvantages of Reaction Injection Molding (RIM)
- Application of Reaction Injection Molding (RIM)
What is Reaction Injection Molding (RIM)?
Reaction Injection Molding (RIM) is a liquid-to-solid polymer molding process.
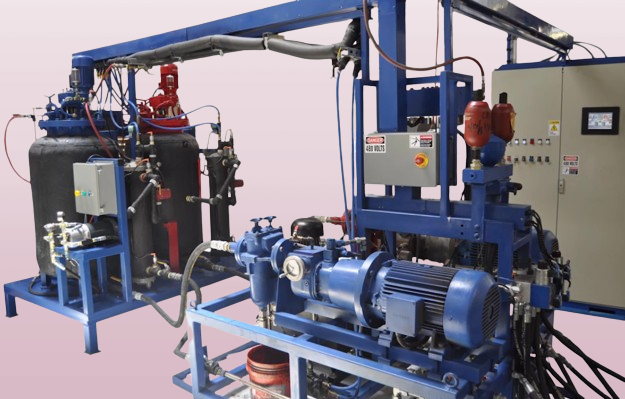
It uses two highly reactive liquid components,
- Polyol (Resin)
- Isocyanate (Hardener)
These two components are mixed and injected into a heated mold under pressure. They undergo a chemical reaction called exothermic reaction which may include degassing or foaming.
The mixture then solidifies within the mold to form a rigid or flexible polyurethane product.
Reaction Injection Molding (RIM) Process:
The step-by-step overview of the reaction injection molding process is
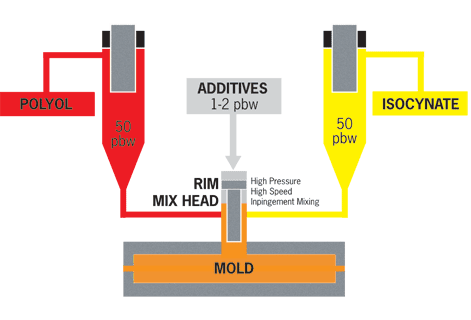
Step:1
The two main components of the reaction injection molding process, polyol and isocyanate, are stored in separate tanks. The polyol is a blend of polyol resin, surfactants, catalysts, and blowing agents. The isocyanate is a reactive liquid that acts as the hardener.
Step:2
The polyol and isocyanate are metered precisely by pumps to ensure the correct ratio of them. The metered polyol and isocyanate are then mixed together in a high-pressure mixing head. The mixing head impinges the two streams together at high velocity.
This creates a turbulent flow that promotes rapid and thorough mixing.
Step:3
The mixed components are injected into a heated mold under low pressure. The mold is made of two halves that are clamped together to form a closed cavity.
Step:4
The polyol and isocyanate undergo exothermic reaction within the mold to form a polymer, called polyurethane polymer. The heat released from the reaction helps to cure the polymer and solidify the part.
Step:5
After curing the mold is opened and the final part is ejected. The part is then allowed to cool further.
Depending on the specific application, there may be additional steps involved in the reaction injection molding process, such as reinforcement, filling or skinning
Thus these are the processes involved in Reaction Injection Molding.
Now, let’s see its advantages and disadvantages.
Advantages of Reaction Injection Molding (RIM)
- RIM’s aluminum molds and tooling cost are typically less expensive than steel molds and tooling cost of other injection molding methods.
- RIM molds heat up and cool down faster. This results in shorter cycle times. This means that RIM can produce parts more quickly and efficiently.
- The RIM process has a low chance of needing secondary finishing operations. That is, RIM produces parts with good surface finish.
- The RIM process has the ability to produce products with high dimensional accuracy.
- RIM has the ability to produce large parts, up to several meters in length. This can be difficult or impossible to be done with other molding methods.
- RIM can be used with a wide range of polyurethane materials. This includes rigid, flexible, and filled materials.
- RIM has a less impact on the environment since it is a relatively energy-efficient process.
- RIM can be used to consolidate multiple parts into a single part. This can reduce assembly time and improve product functionality.
In summary,
Reaction Injection Molding (RIM) is a versatile and cost-effective manufacturing process. Therefore offering a wide range of advantages over producing high-quality plastic parts.
Disadvantages of Reaction Injection Molding (RIM)
- The raw materials used in the RIM process, such as polyols and isocyanates, are relatively expensive compared to other molding materials.
- The RIM polymer needs to fully cure before the mold can be opened. This leads to longer demolding times.
- The RIM process is sensitive to moisture and temperature. Exposure to moisture can prematurely cure the polymer. And exposure to high temperatures can cause the polymer to degrade
- The RIM process can emit hazardous fumes, such as isocyanates and amines. These fumers can be harmful to workers if they are not properly ventilated.
- RIM parts are typically not recyclable due to the complex chemical structure of polyurethane.
Overall,
Reaction Injection Molding (RIM), is an effective and valuable manufacturing process that is widely used by various industries. However, it is crucial to consider its limitations and disadvantages before making a decision about whether or not to use this process.
Materials undergo Reaction Injection Molding (RIM)
The primary materials undergo the reaction injection molding process are
Polyols:
Polyols are the hydroxyl-containing compounds. They form the backbone of the polyurethane polymer.
Common examples of polyols used in RIM include,
- Polyether polyols
- Polyester polyols
- Castor oil-based polyols
Isocyanates:
Isocyanates are the reactive molecules. It crosslinks with the hydroxyl groups in polyols to form the polyurethane polymer.
The two types of isocyanates used in the RIM process are,
- Aromatic isocyanates
- Aliphatic isocyanates
Blowing Agents:
Blowing agents are incorporated into RIM systems to create a cellular or foam structure within the polyurethane product.
Common blowing agents include:
- Water
- Hydrazines
- Formic acid
Catalysts:
Catalysts are added to RIM systems to accelerate the curing reaction between polyols and isocyanates.
Common catalysts used in the RIM process include:
- Tertiary amines
- Tin catalysts
- Organophosphorus catalysts
Surfactants:
Surfactants are added to RIM systems to improve the wettability and the flow of the polymer.
Commonly used surfactants in the RIM process include:
- Polyether glycols
- Silicone-based surfactants
- Fluorinated surfactants
Release agents:
Release agents are applied to the mold surfaces to prevent the cured polymer from sticking to the mold.
Some common release agents that are used in RIM include,
- Silicone-based release agents
- Wax-based release agents
- Fluorinated release agents
In addition to these primary materials, various additives can be incorporated into RIM systems to achieve specific properties.
Application Of Reaction Injection Molding (RIM)
Automotive parts:
The impact-absorbing and lightweight properties of RIM make it ideal for manufacturing automotive parts, such as,
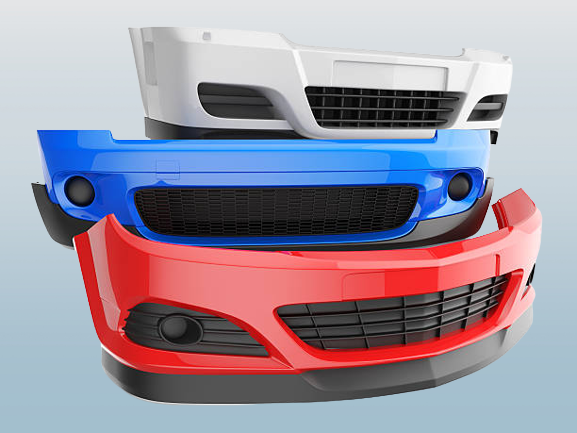
- Interior trim
- Door panels
- Side panels
- Instrument panels
- Bumpers
- Fascias
- Spoilers
Structural components:
RIM’s properties such as structural integrity and dimensional accuracy make it ideal for manufacturing structural components, such as,
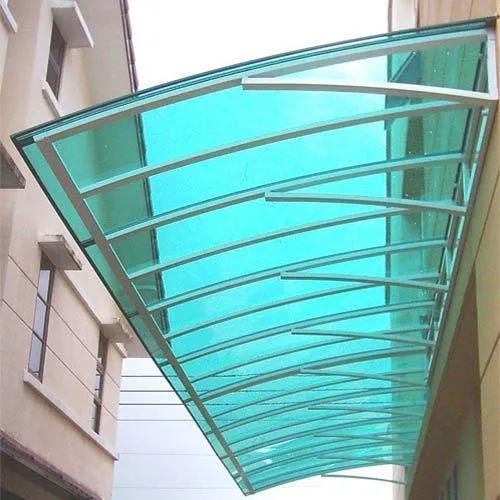
- Roofing components
- Building panels
- Window frames
- Furniture components
- Appliance housings
Electrical enclosures:
RIM’s electrical insulating properties makes it ideal for manufacturing electrical enclosures, such as,
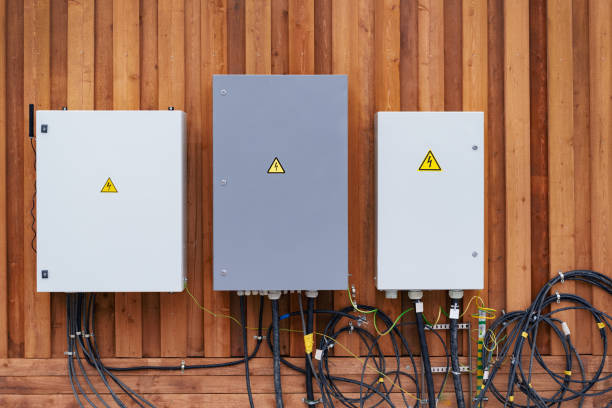
- Junction boxes
- Control panels
- Meter enclosures
- Electrical boxes
- Switchgear housings
Appliance housings
RIM’s properties such as, resistance to heat, moisture, and chemicals makes it ideal for manufacturing products like,
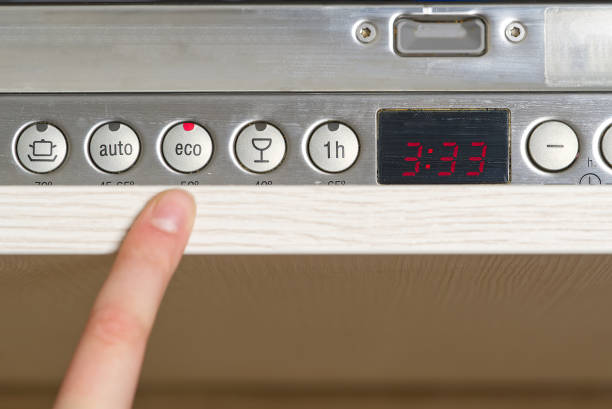
- Refrigerator doors
- Microwave housings
- Air conditioner housings
- Washing machine cabinets
- Dishwasher panels
Medical devices:
RIM’s biocompatibility and ability to meet stringent medical standards makes it ideal for manufacturing medical components, such as,
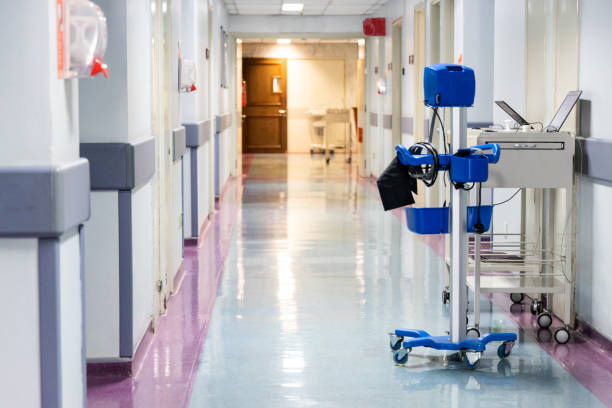
- Medical carts
- CT scanner enclosures
- MRI scanner housings
- Dialysis machine components
- Surgical instrument housings
Sporting Goods:
RIM’s durability and lightweight properties make it ideal for manufacturing sporting goods, such as,
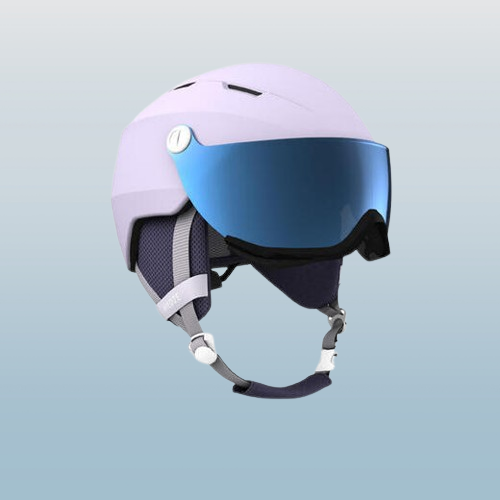
- Bicycle components
- Skateboard decks
- Ski helmets
- Snowboard bindings
- Protective gear
Toys:
RIM’s ability to produce colorful and durable parts with smooth surfaces, makes it ideal for manufacturing toys like,
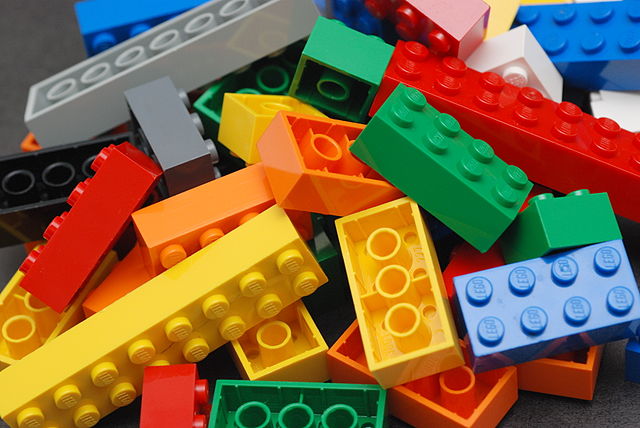
- Ride-on toys
- Construction toys
- Educational toys
- Playsets
- Action figures
In summary,
Reaction Injection Molding (RIM) is a versatile manufacturing process that has the ability to produce high-quality and durable parts. Therefore it has diverse applications in various industries.
Conclusion
In conclusion, despite its advantages and disadvantages, RIM is a valuable technique in the realm of plastic molding.
As technology advances, RIM continues to evolve, presenting new opportunities for innovative applications and improved product development.
Learning and embracing RIM can lead to enhanced product quality and accelerated production timeliness.
How TOPGRID can help you:
We TOPGRID, your manufacturing partner, offer you 50+ such manufacturing processes. You can choose as per your product needs.
We’re dedicated to upholding the highest standards of quality throughout every stage of your manufacturing process.
From the initial design to the final product completion, we ensure the materials that undergo these processes and the products produced are quality-checked.
Topgrid – Injection Molding Service
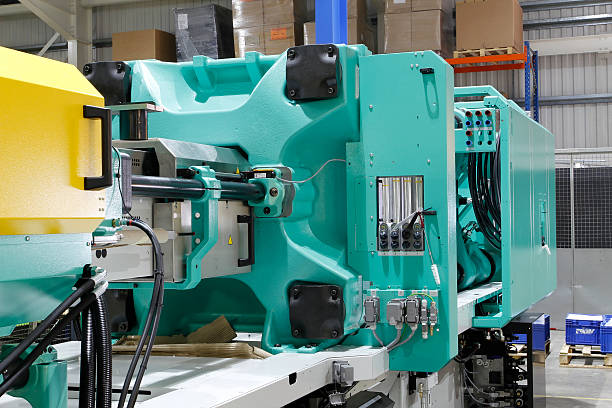
- At Topgrid, we pride ourselves on being a best provider of Plastic Injection Molding Services.
- With a strong commitment to precision, innovation, and customer satisfaction, we are your trusted partner for all your plastic injection molding needs.