Introduction
Compression molding plays a vital role in manufacturing processes. Compression molding is a manufacturing process in which material is placed in a mold. The mold is then closed, heated, and compressed to get the desired form.
Various production companies from small to big employ compression molding techniques to manufacture a wide variety of their products. Various products from vehicle parts to kitchen tools are often manufactured using compression molding processes.
Topgrid Provide you with end-to-end manufacturing services, from the initial stage to final product delivery. At TOPGRID we provide you with 2200+ vendors and 760+ consultants. You can choose according to your ultimate need.
We have worked on more projects in the Compression molding process. In this article, we have given you a clear and concise explanation of all you need to know about the Compression molding process.
In this article, we’ll see,
- What is compression molding? Definition
- Compression molding Process
- What are the materials used in compression molding?
- Products and applications of compression molding.
- Types of compression molding machine.
- Advantages of compression molding.
- Disadvantages of compression molding
- Topgrid’s Compression Molding Services
What is Compression Molding? Definition:
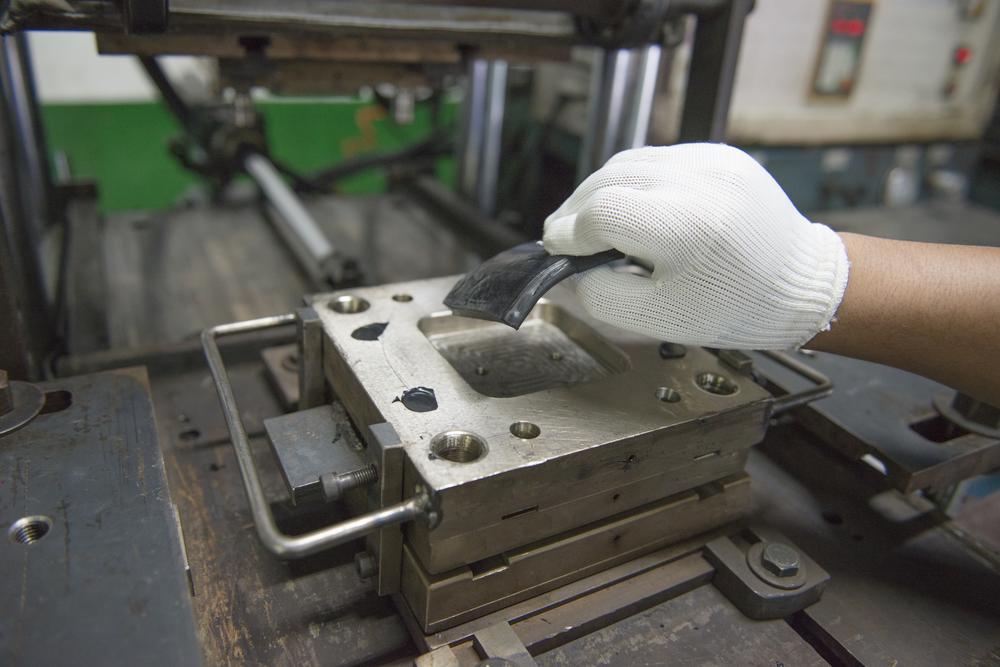
Compression molding is a manufacturing process that involves shaping materials. Heat and pressure are applied to a pre-measured quantity of material within a mold cavity. This results in the production of a solid and durable product with the desired shape.
Compression Molding Process:
The step-by-step compression molding process works as follows,
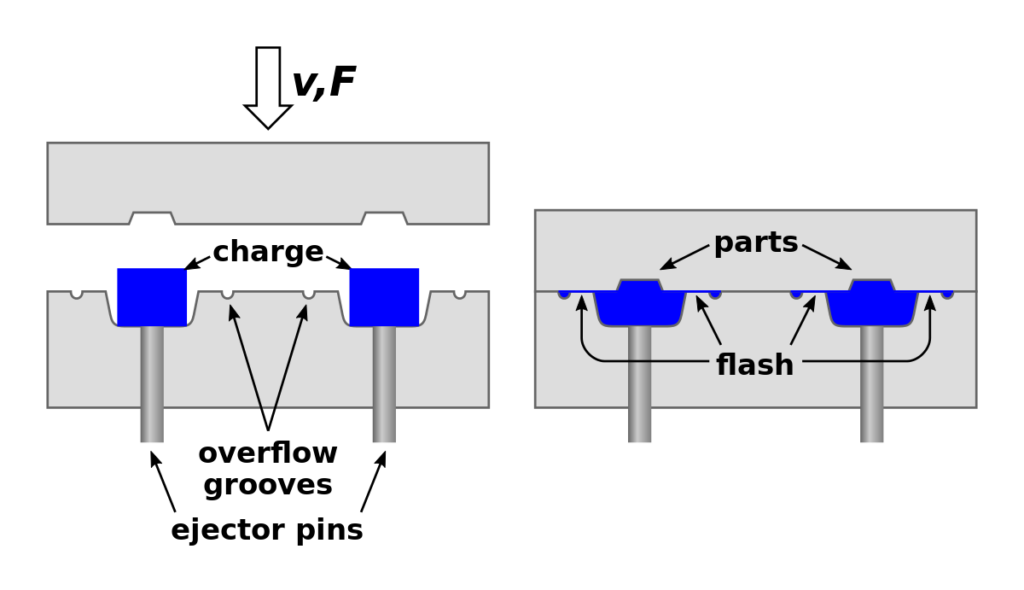
1. Creating Molds:
Depending on factors like the type of mold needed, the material to be molded, the quantity of the parts required, and available resources, molds are produced by various methods like die casting, 3D printing, and CNC machining.
2. Preparing the material:
The process involves the selection and preparation of the material. This can include mixing raw materials, such as resins, fillers, and additives. This creates a compound suitable for molding.
3. Placing material in the mold:
The mold consists of two halves, the upper movable mold half and the lower fixed mold half. The prepared material is placed in the lower fixed mold half.
4. Closing the mold:
The mold is closed, and pressure is applied. The material is compressed and evenly distributed within the mold cavity.
5. Heating the mold:
Heat is applied to the closed mold. This heating stage activates a chemical reaction in materials, causing them to harden and take the desired shape. This stage may also involve the application of pressure, which varies depending on the specific material and product.
6. Curing:
The Curing part of the molding process involves lowering the temperature and smoothening the hardening of the compressed materials into the final product.
7. Cooling:
After the curing process is complete, the mold is cooled to allow the material to solidify and maintain its shape.
8. Releasing the material:
After the cooling process, the final product is removed from the mold. The resin flash around the edges must be manually cut off or removed and the product may need to be cleaned before further processing or use.
At TOPGRID, we keep track of every manufacturing stage and provide you with timely order updates.
What are the materials used in Compression Molding?
Here are the top 5 materials that are commonly used in compression molding in various industries.
1. Epoxyl:
- Epoxy is widely used in compression molding processes.
- It is popular in compression molding due to its mechanical properties like high tensile, flexural strength, long-lasting, Minimal shrinkage, Excellent electrical insulating properties
- Due to these properties, it is used in manufacturing components such as composite panels, brackets, and more, that are used in industries like aerospace and automotive.
2. Melamine:
- Melamine’s heat resistance, hardness, chemical resistance, and durability make it a popular choice for the compression molding process.
- It can be easily colored and molded and provides a smooth and glossy finish, which is why used in the production of items such as dinnerware, kitchenware, and decorative laminates
- Melamine looks good and works well with its functional properties, making it a great choice for both consumer and industrial applications.
3. Silicone:
- Silicone is a commonly used material for compression molding due to its unique properties like flexibility and elasticity, heat resistance, chemical resistance, and excellent electrical insulating properties.
- It can withstand a wide range of temperatures from extreme cold to high heat without losing its properties.
- It can also withstand exposure to UV radiation and harsh weather conditions, which is valuable in outdoor applications.
- Products like seals and gaskets, medical devices, kitchenware, and laboratory equipment are manufactured using melamine.
- Even baby products like pacifiers, teething toys, and bottle nipples are manufactured using melamine.
4. Urethane:
- Urethane, also known as polyurethane, is an adaptable material used in compression molding for making a wide variety of products.
- Urethane’s versatility, ranging from soft to rigid formulations, and its durability, impact resistance, and chemical resistance, make it a popular choice in compression molding.
- Products like wheels, rollers, seals and gaskets, and bumpers and bushings in industrial equipment are manufactured using urethane.
5. High-Density Polyethylene (HDPE):
- High-density polyethylene is a thermoplastic material, commonly used in compression molding.
- HDPE offers a cost-effective way to produce a wide range of products for different industries.
- It is known for its lightweight, rigidity, and high resistance.
- Bottles and containers, components like battery cases, fuel tanks, and items such as plastic toys are manufactured using high-density polyethylene (HDPE).
Several other materials that are used in compression molding are,
- Polyamide-imides (PAIs)
- Polyether ether ketone (PEEK)
- Polyurethane (PU)
- Polyphenylene sulfide (PPS)
- Phenolic resins (PF)
- Polytetrafluoroethylene (PTFE)
- Urea-formaldehyde (UF)
- Diallyl phthalate (DAP)
At Topgrid, we ensure all the materials are quality-checked throughout every stage of manufacturing to meet or exceed your expectations of receiving products.
Products and Applications of Compression Molding:
Compression molding has found its application in various industries. Some of the products and parts that are manufactured using compression molding are as follows:
1. Automotive Parts
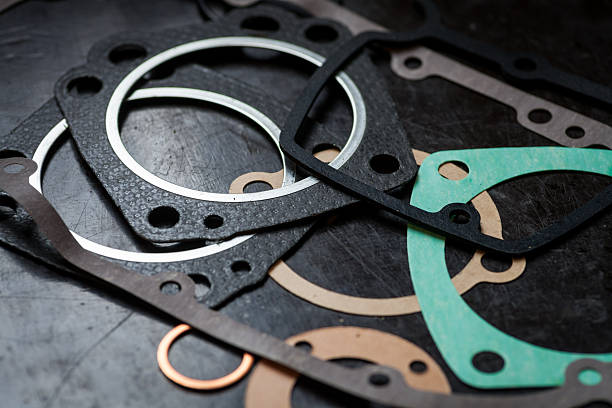
Due to its cost-effectiveness and the ability to create complex shapes, compression molding is used to produce automotive components like,
- Gaskets
- Seals
- Bumpers
- Interior trim parts for vehicles.
2. Aerospace Components:
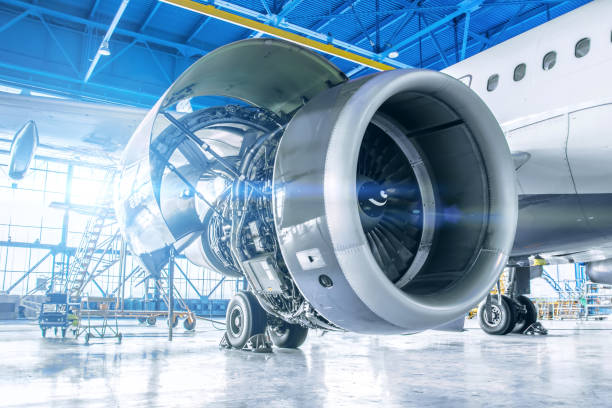
Due to its performance standards and ability to meet safety standards, compression molding is used to produce aerospace components like,
- Aircraft interiors
- Insulation
- Structural components.
3. Electrical and Electronics Products:
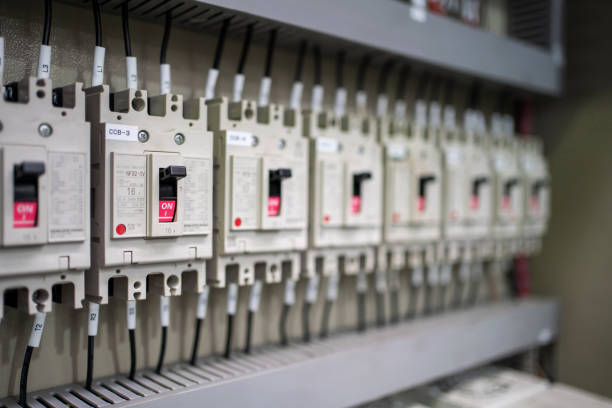
Due to its excellent electrical insulating properties, compression molding is used in manufacturing electrical and electronic products like,
- Electrical insulation components
- Circuit breakers
- Connectors.
4. Medical Products:
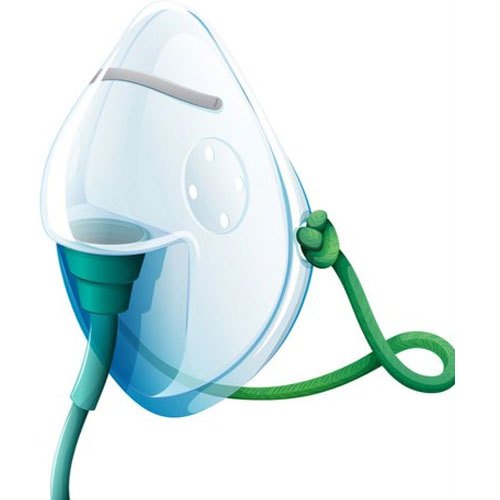
Using biocompatible materials, compression molding is employed in manufacturing medical products like,
- Prosthetic parts
- Surgical instruments
- dental devices.
5. Consumer goods:
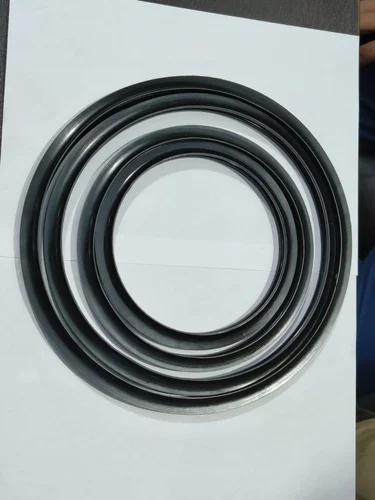
Due to its ability to produce consistent, high-quality items and cost efficiency, compression molding is used in manufacturing various plastic products like,
- Kitchenware
- Toys
- Bottle caps
6. Construction materials:
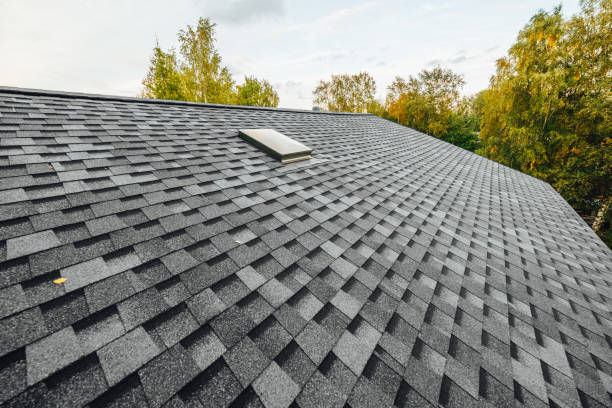
Due to its ability to create intricate surface textures, compression molding is used to manufacture construction items like,
- Bricks
- Roof tiles
- Decorative panels
7. Sporting goods:
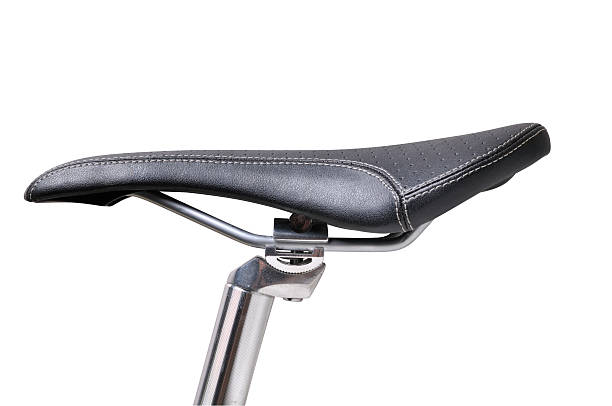
Due to its durability and performance, compression molding is used to manufacture sports equipment like,
- Skateboards
- Bicycle saddles
- Helmet liners
8. Laminates:
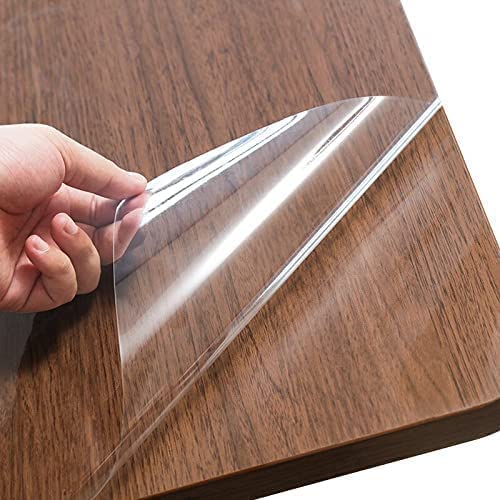
Compression molding is employed to produce laminates for
- Tabletops
- Countertops
- Decorative surfaces
Compression molding’s ability to efficiently create complex shapes it is suitable for a wide range of materials, including thermoplastics, thermosetting resins, rubber, and composites. This makes it a valuable manufacturing method across multiple industries.
We at Topgrid served various industries that manufacture these products and completed over 130+ projects.
Hence we can be your best manufacturing partner who turns your manufacturing challenges into success stories no matter what your industry is!
Types of Compression molding machines:
Based on specific applications and requirements several types of compression molding machines are designed.
1. Hydraulic compression molding machine:
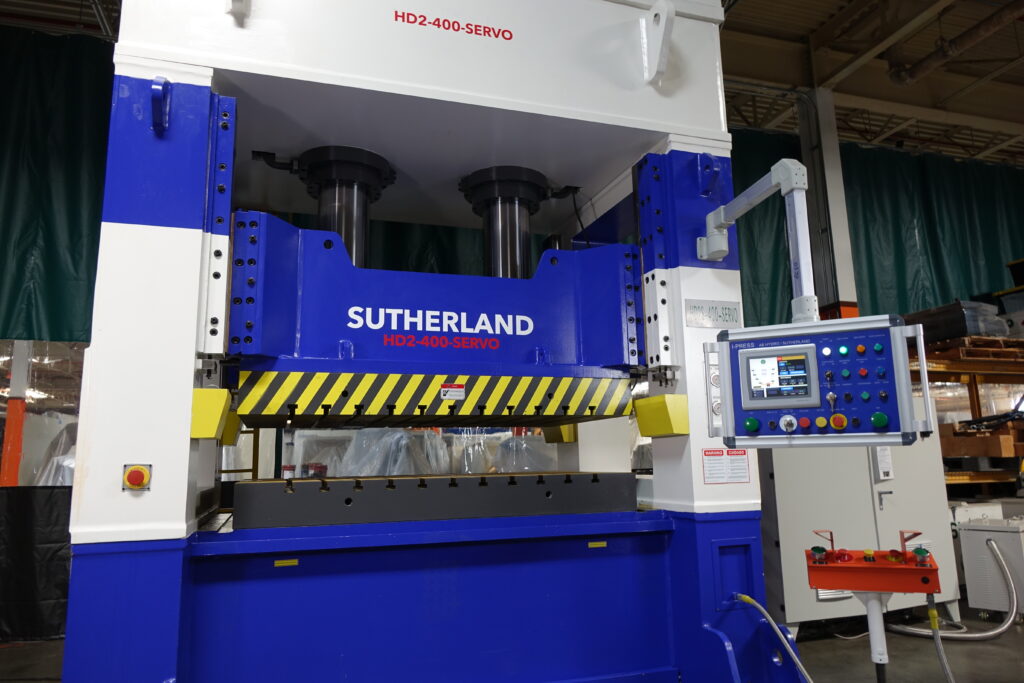
- Uses hydraulic systems to generate the pressure required for the molding process.
- Known for their precision and ability to provide high-pressure control.
2. Mechanical compression molding machine:
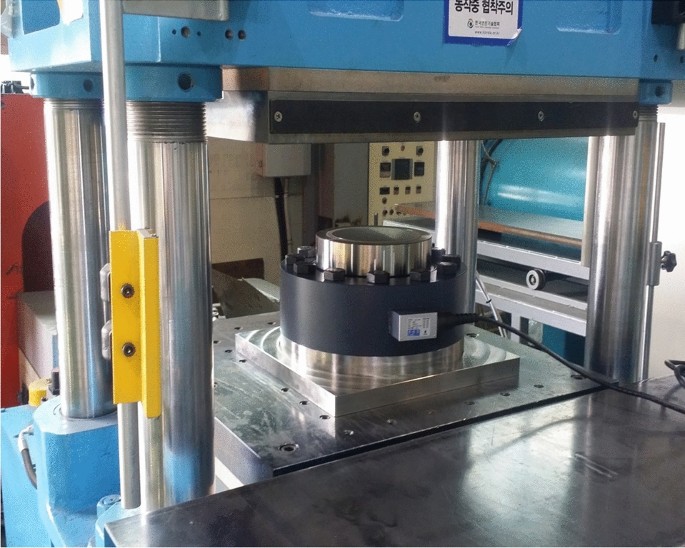
- Uses mechanical linkage to apply force for the molding process
- Chosen for applications that don’t require extremely high pressures and where mechanical force is sufficient.
3. Pneumatic compression molding machine:
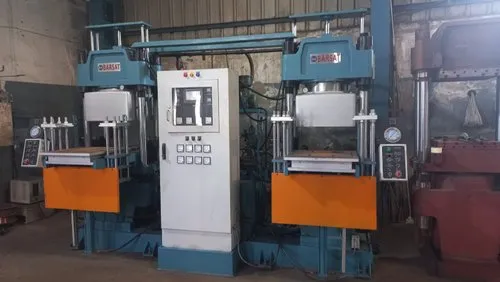
- Uses compressed air to provide the force needed for compression molding.
- Chosen for applications that require lower pressure and where precise control of pressure is not as critical.
4. Vacuum compression molding machine:
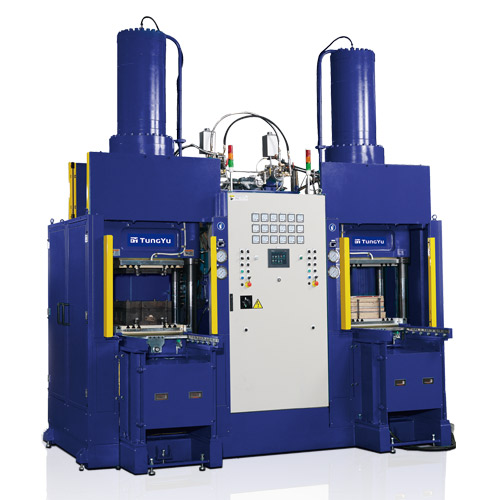
- Uses vacuum technology to improve the distribution of material within the mold.
- Chosen for applications that require void-free, high-quality parts.
5. Vertical compression molding machine:
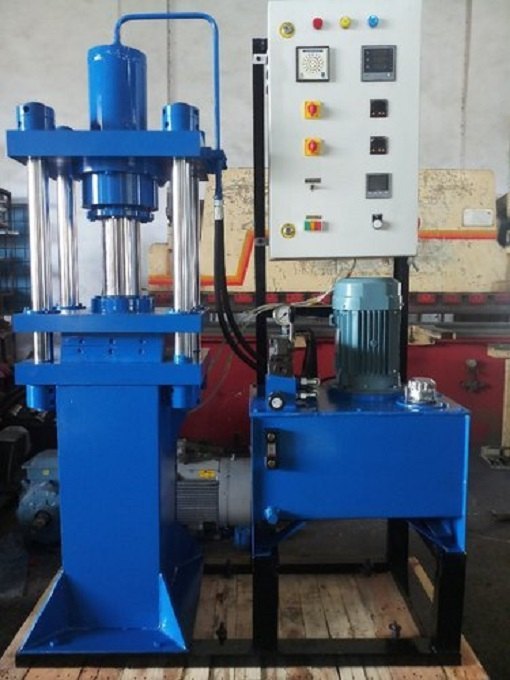
- Uses vertical presses that have a vertical orientation.
- Advantageous for certain applications where the part geometry or tooling setup is better suited to a vertical configuration.
6. Horizontal compression molding machine:
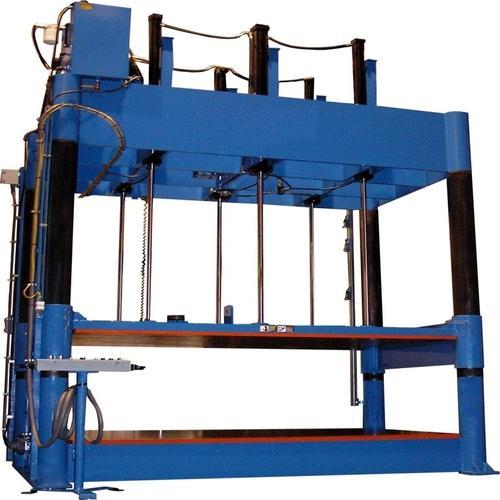
- Uses horizontal presses that have a horizontal orientation.
- Used for molding large and flat parts.
7. Laboratory and small-scale compression molding machines:
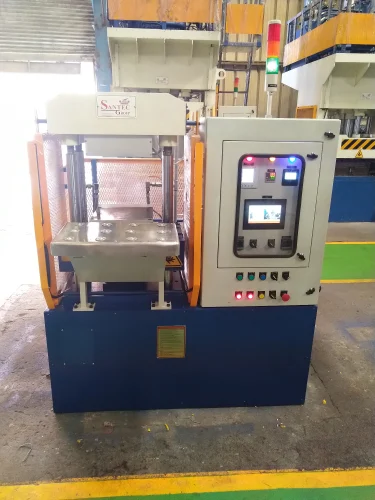
- Compact and benchtop machines.
- Takes up less space than large industrial compression machines but is well-suited for large runs.
- Find its applications in research, development, and low-volume production settings.
Therefore these are the compression molding machines used by manufacturers widely.
Manufacturers select the most suitable machine based on the specific requirements of the application including type of material, part size, required pressure, and production volume.
Advantages of the compression molding process:
- Compression molding is a cost-effective manufacturing method compared to other processes like injection molding. It requires less machinery and energy.
- Compression molding is design flexibility. It allows for complex part designs and intricate details.
- Compression molding is material compatibility, therefore it works well with a variety of materials including thermosetting plastics, rubber, composites, and more.
- Products manufactured using compression molding tend to have high strength and durability.
- Compression molding generates less material waste, reducing material costs and environmental impact.
- Compression molding has a shorter cycle time, resulting in quicker production.
Disadvantages of the compression molding process:
- As it has a relatively slower cycle time it may not be suitable for high-volume production.
- Compression molding is often a manual or semi-automated process.
- Achieving a high-quality surface finish can be more challenging in compression molding. May require additional finishing steps.
- It is not suitable for all complex designs.
- The initial tooling and mold costs for compression molding can be relatively high, making it less cost-effective for small-scale production
Compression molding offers several advantages and disadvantages. It plays a vital role in manufacturing units based on the specific requirements of the product and production volume.
Conclusion:
Compression molding is one of the oldest manufacturing techniques that are still employed by various manufacturing industries due to its efficiency and effectiveness.
We hope this blog gave you the required information about the compression molding process.
our Topgrid team is here to help you if you’re facing various challenges in these manufacturing processes. We’re your manufacturing partner who turns your manufacturing challenges into success stories.
Topgrid – Compression Molding Service
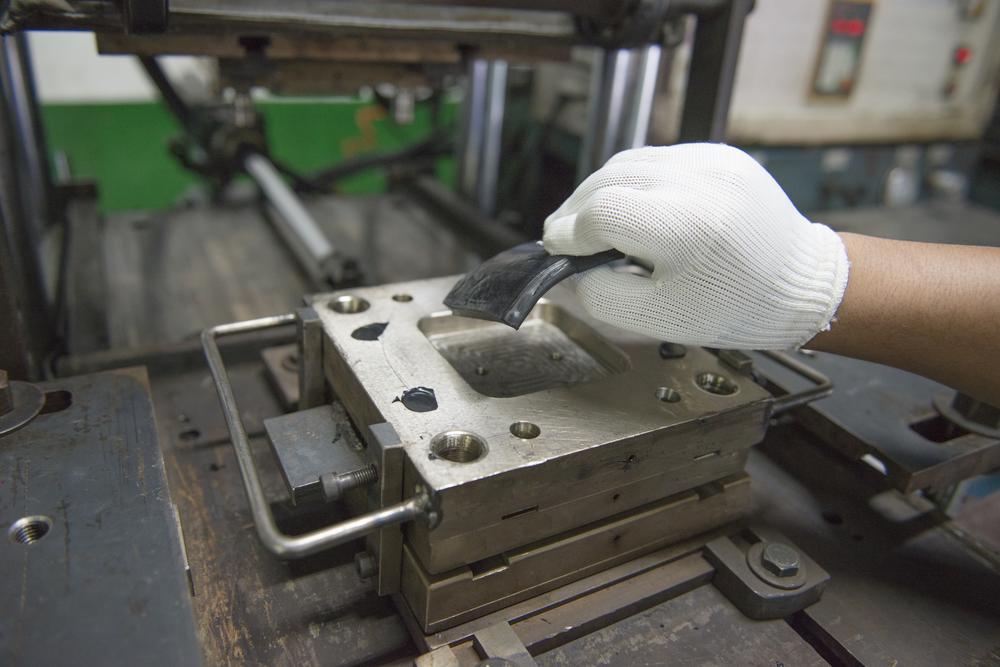
- At Topgrid, we take immense pride in being a best provider of Compression Molding Services.
- Topgrid’s experienced engineers can help you design and manufacture custom molds to meet your specific needs.
- Topgrid’s experienced engineers can help you design and manufacture custom molds to meet your specific needs that optimizes quality and efficiency.
Related Blogs
Centrifugal Casting – Definition, Process, Types and Applications
Centrifugal casting is a versatile and efficient metal casting process used to create high-quality, thin-walled cylindrical parts. It uses centrifugal force…
Semi Centrifugal Casting – Definition, Process, Advantages and Applications
Semi centrifugal casting is a specialized metal casting process that combines gravity pouring with centrifugal force to produce high-quality castings. …
Low Pressure Die Casting – An Overview
Low pressure die casting (LPDC) is one of the metal casting processes. It uses low pressures to force molten metal…